Making of …
Auf dieser Seite wollen wir einmal ein kleinen Einblick „hinter die Kulissen“ geben. Das heißt, dass wir einmal zeigen wollen, welche Arbeitsschritte zur Herstellung vermeintlich „einfacher“ Produkte nötig sind. Wir hoffen damit unsere Kunden etwas über die vielfältigen Fertigungsschritte der Artikel informieren zu können und damit dann vielleicht auch etwas Verständnis für Lieferzeiten und Preise wecken zu können. Vielleicht könnte man einige Schritte zur Herstellung der Produkte wie z.B. das Entgraten von Blechen weglassen. Da diese Arbeitsweise jedoch nicht mit unseren Qualitätsgrundsätzen vereinbar ist, werden wir auch weiterhin alle Fertigungsschritte ausführen, die für eine hohe Produktqualität unerläßlich sind. Denn wir wissen : „Der Ärger über fehlende Qualität hält länger an als die Freude über einen niedrigen Preis“.
Gute Unterhaltung bei diesen Fertigungseinblicken.
Fertigung eines Messing-Schildes für eine Aktenmappe
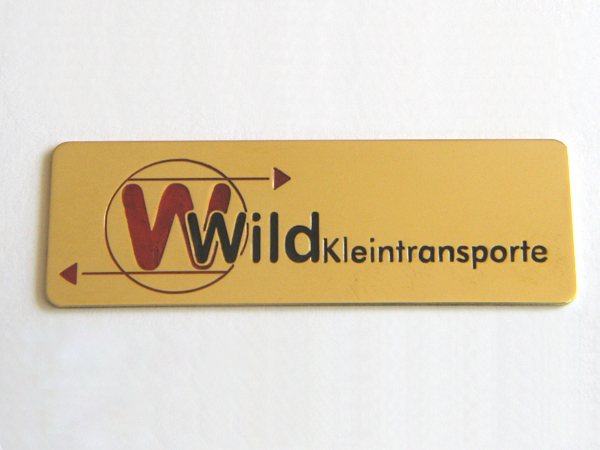
Dieses Messingschild soll für eine Aktenmappe erstellt werden.
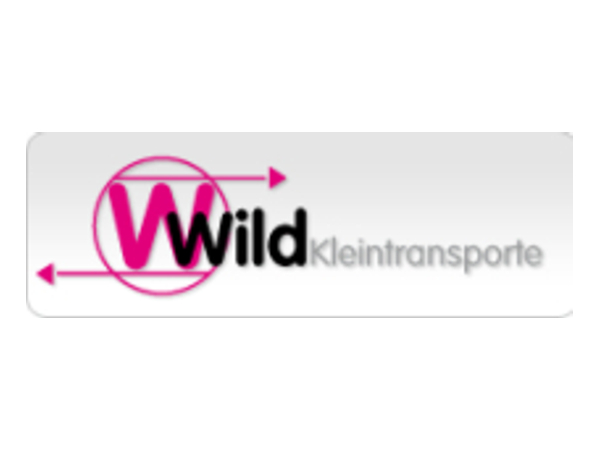
Das ausgedruckte Kundenlogo ist die Vorlage für das Schild.
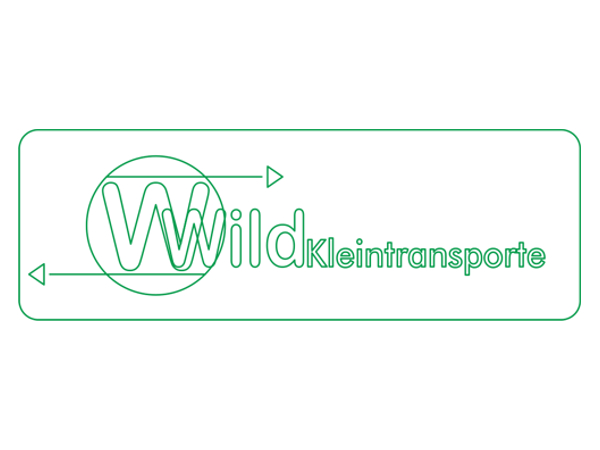
Da der Ausdruck nicht gefräst werden kann, wird er zunächst digitalisiert. Das bedeutet, dass er für eine neue Datei manuell in Linien umgewandelt wird, die der Fräser später abfahren kann.
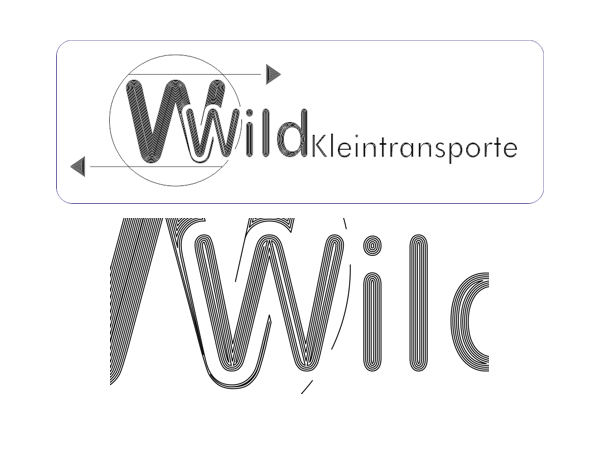
Um das Logo mit allen Details darzustellen, müssen die Buchstaben mit einem sehr feinen Fräser graviert werden. Das Bild zeigt, wie viele sich überlappende Fräsbahnen hierzu erstellt werden müssen.
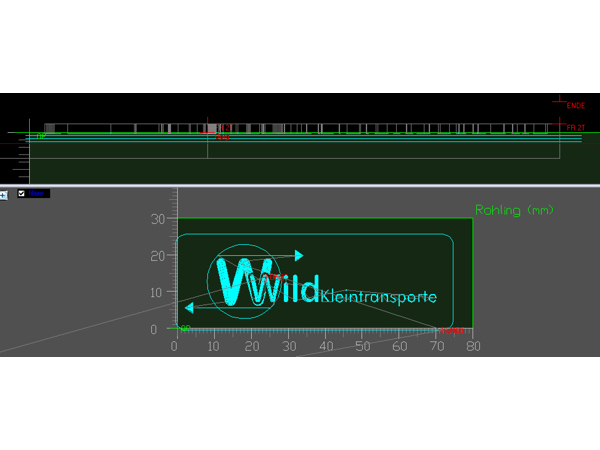
Im nächsten Schritt muss das erstellte Layout in eine für die Fräse lesbare Datei gewandelt werden. Dies bedeutet, dass jetzt auch der verwendete Fräser, Drehzahl, Vorschub und weitere Maschinenparameter erstellt und gespeichert werden.
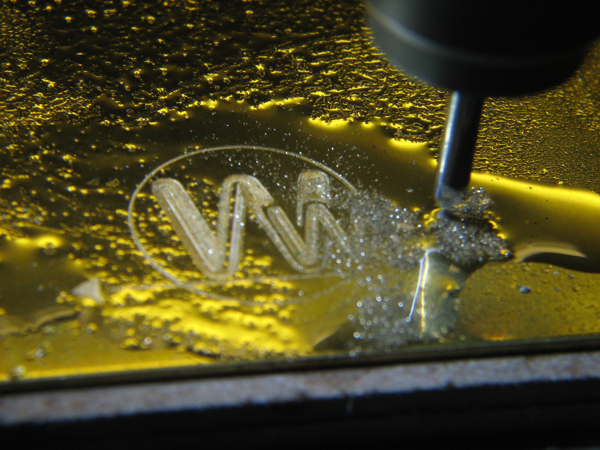
Nun kann endlich die Gravur ausgeführt werden.
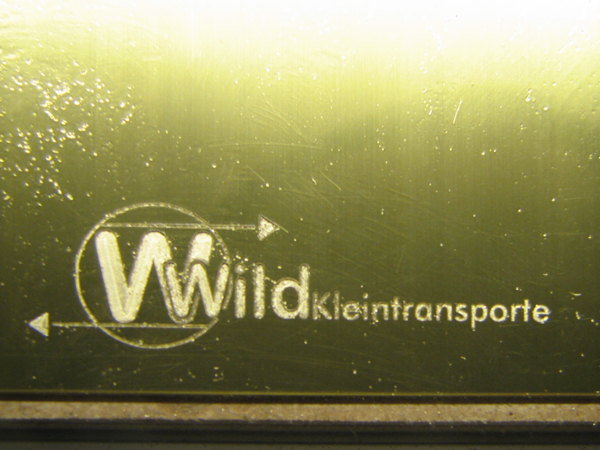
In der fertigen Gravur des Logos sind kleine Stege erhalten geblieben, damit später die beiden Farben nicht ineinanderlaufen.
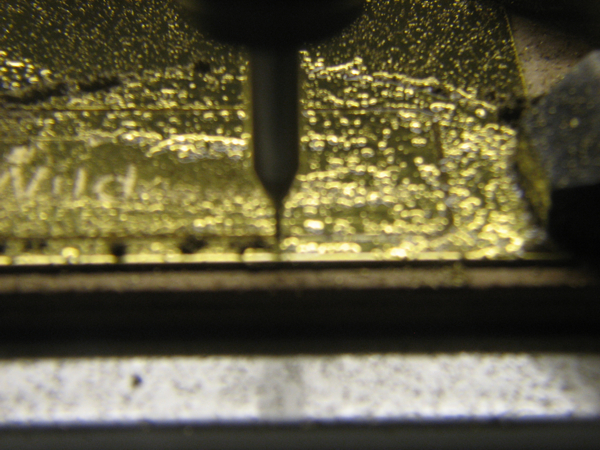
Jetzt kann die Kontur des Schildes ausgefräst werden.
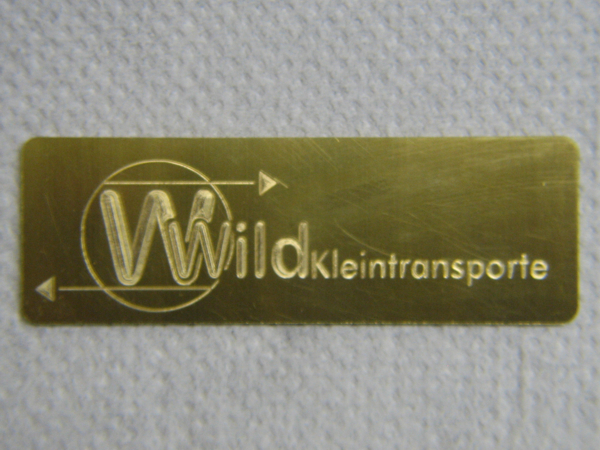
Das Schild ist fertig. Leider hat es durch die Bearbeitung einige Kratzer abbekommen und die Kanten haben noch einen scharfen Grat. So kann es nicht abgeliefert werden.
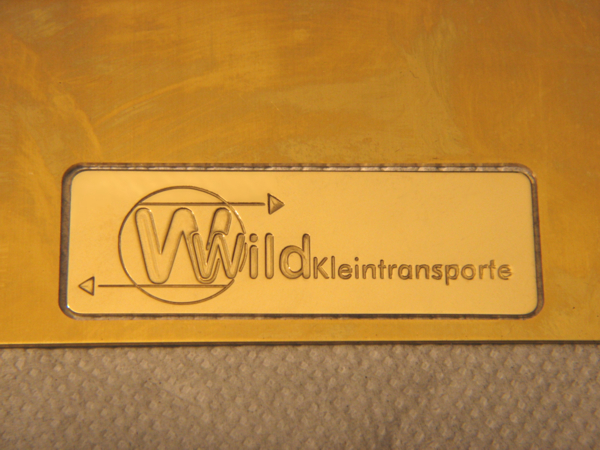
Das Schild muss entgratet und poliert werden. Der Unterschied ist im Vergleich zum Rest des Bleches gut zu sehen.
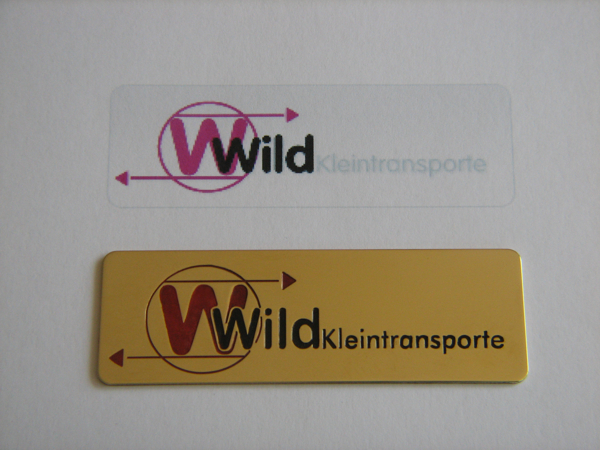
Nachdem die Schrift mit Farbe ausgelegt wurde, ist das Schild nun endlich fertig und muss einen Vergleich mit der Vorlage nicht scheuen.
Fertigung eines Messing-Schildes für eine Aktenmappe (1/11)
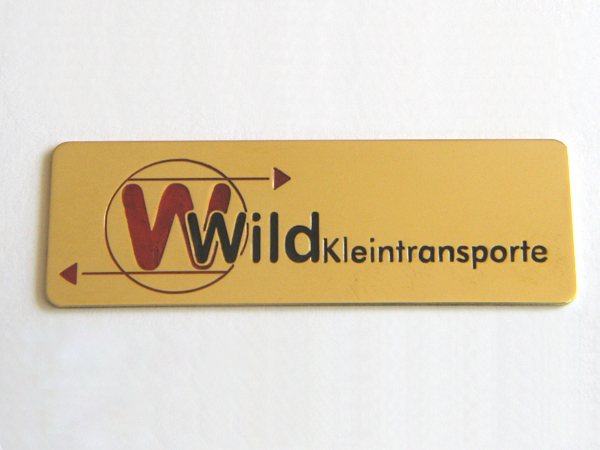
Dieses Messingschild soll für eine Aktenmappe erstellt werden.
Fertigung eines Messing-Schildes für eine Aktenmappe (2/11)
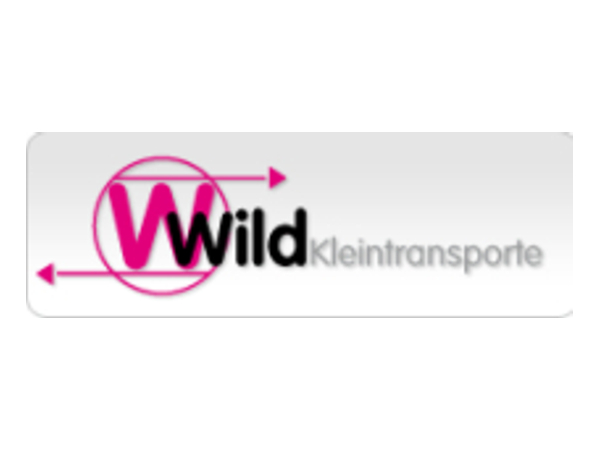
Das ausgedruckte Kundenlogo ist die Vorlage für das Schild.
Fertigung eines Messing-Schildes für eine Aktenmappe (3/11)
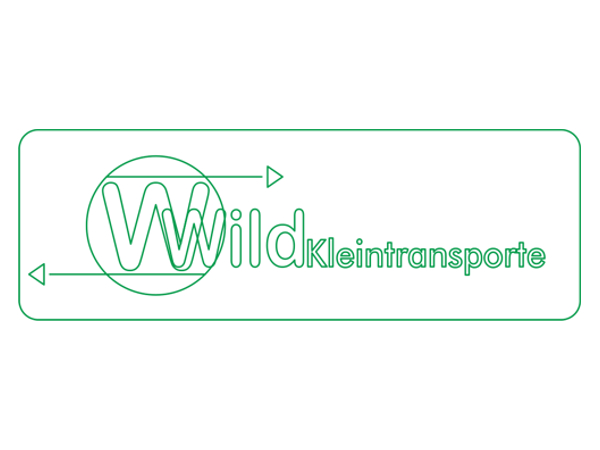
Da der Ausdruck nicht gefräst werden kann, wird er zunächst digitalisiert. Das bedeutet, dass er für eine neue Datei manuell in Linien umgewandelt wird, die der Fräser später abfahren kann.
Fertigung eines Messing-Schildes für eine Aktenmappe (4/11)
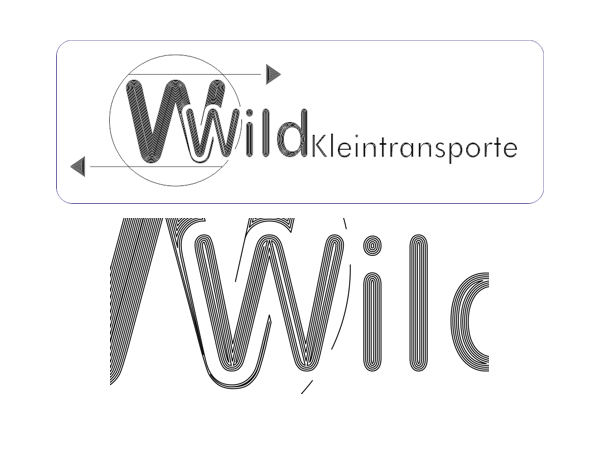
Um das Logo mit allen Details darzustellen, müssen die Buchstaben mit einem sehr feinen Fräser graviert werden. Das Bild zeigt, wie viele sich überlappende Fräsbahnen hierzu erstellt werden müssen.
Fertigung eines Messing-Schildes für eine Aktenmappe (5/11)
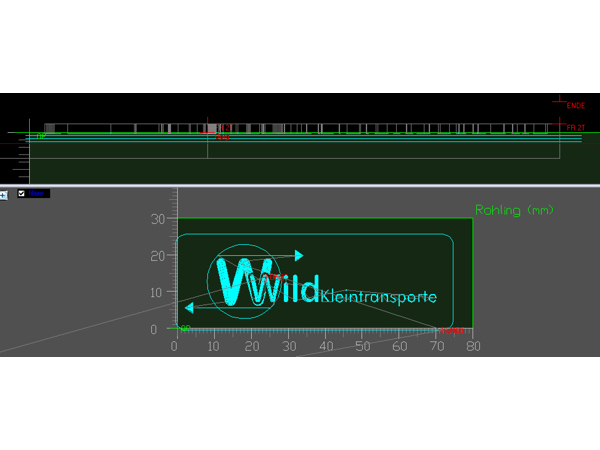
Im nächsten Schritt muss das erstellte Layout in eine für die Fräse lesbare Datei gewandelt werden. Dies bedeutet, dass jetzt auch der verwendete Fräser, Drehzahl, Vorschub und weitere Maschinenparameter erstellt und gespeichert werden.
Fertigung eines Messing-Schildes für eine Aktenmappe (6/11)
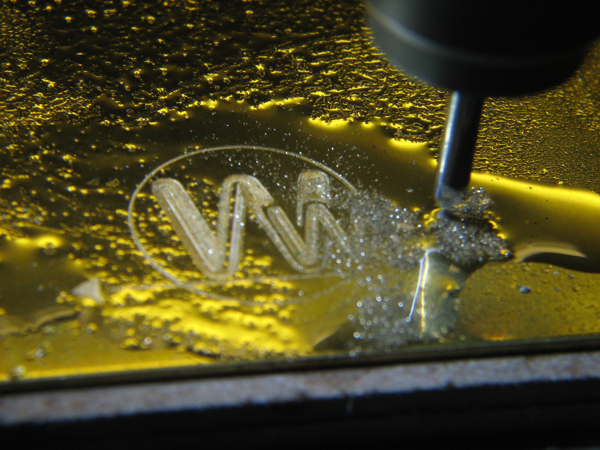
Nun kann endlich die Gravur ausgeführt werden.
Fertigung eines Messing-Schildes für eine Aktenmappe (7/11)
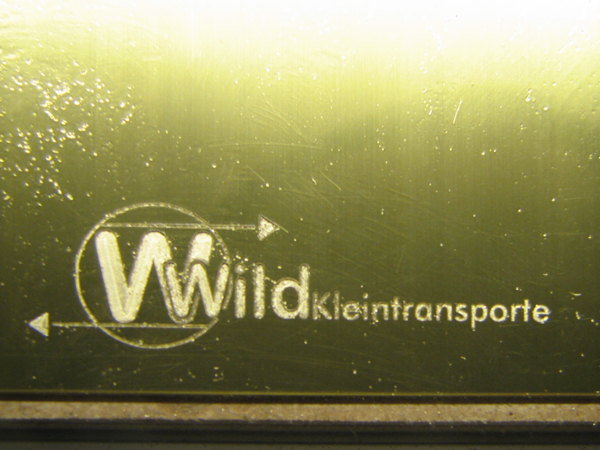
In der fertigen Gravur des Logos sind kleine Stege erhalten geblieben, damit später die beiden Farben nicht ineinanderlaufen.
Fertigung eines Messing-Schildes für eine Aktenmappe (8/11)
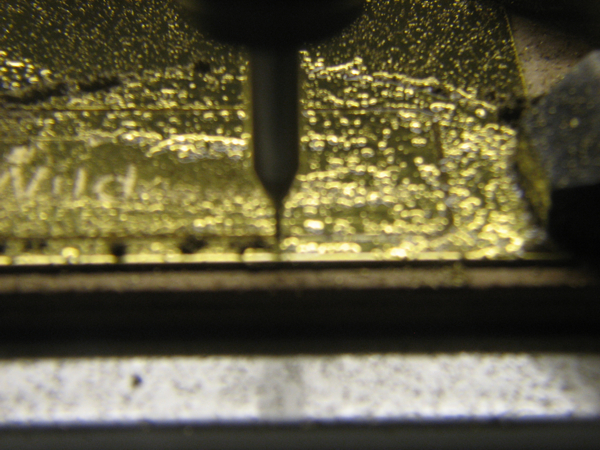
Jetzt kann die Kontur des Schildes ausgefräst werden.
Fertigung eines Messing-Schildes für eine Aktenmappe (9/11)
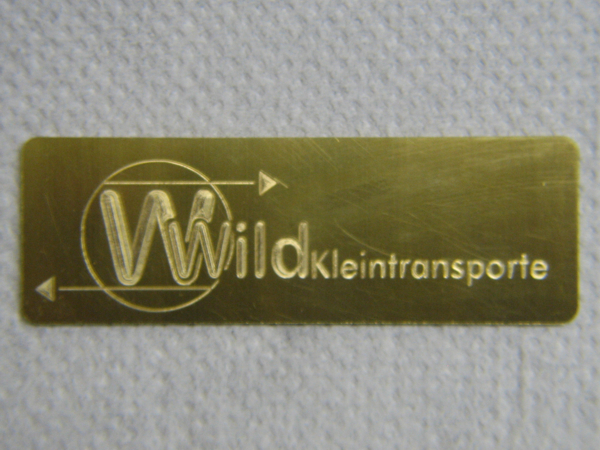
Das Schild ist fertig. Leider hat es durch die Bearbeitung einige Kratzer abbekommen und die Kanten haben noch einen scharfen Grat. So kann es nicht abgeliefert werden.
Fertigung eines Messing-Schildes für eine Aktenmappe (10/11)
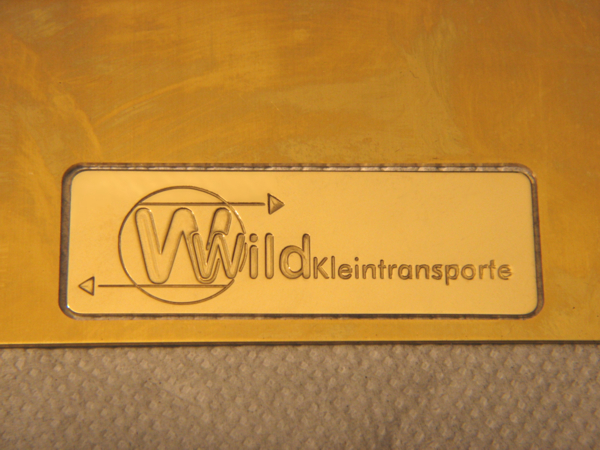
Das Schild muss entgratet und poliert werden. Der Unterschied ist im Vergleich zum Rest des Bleches gut zu sehen.
Fertigung eines Messing-Schildes für eine Aktenmappe (11/11)
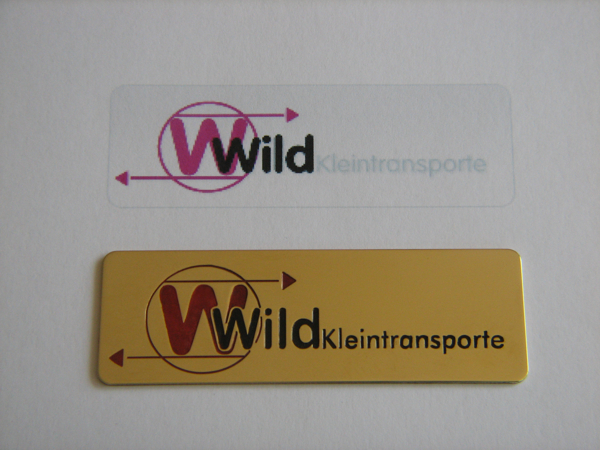
Nachdem die Schrift mit Farbe ausgelegt wurde, ist das Schild nun endlich fertig und muss einen Vergleich mit der Vorlage nicht scheuen.
Fertigung eines Rahmens für einen Tonabnehmer
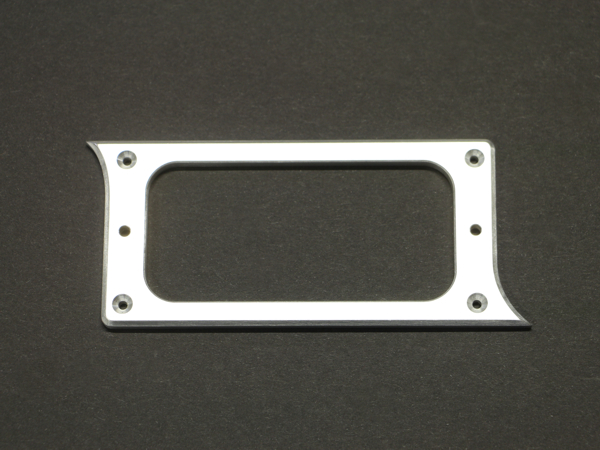
Dieser Rahmen soll für einen Tonabnehmer einer Gitarre gefräst werden.
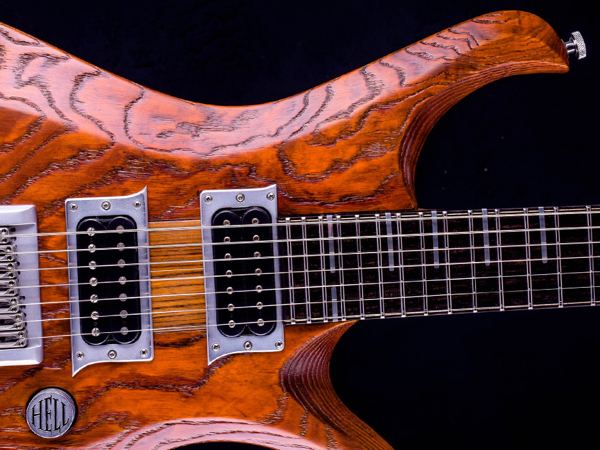
So wird er später einmal mit dem Tonabnehmer auf der Gitarre sitzen.
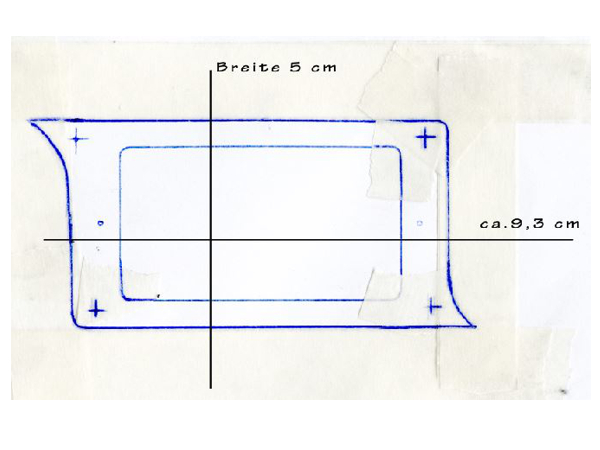
Ausgangspunkt für den Rahmen ist die Zeichnung des Kunden.
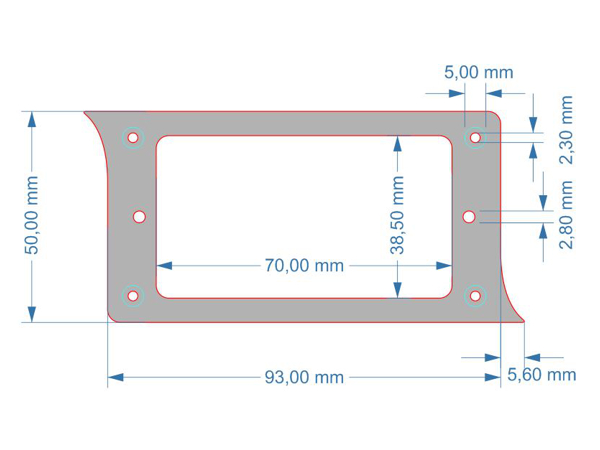
Auf Basis der Kundenzeichnung wird nun in eine bemaßte CAD-Zeichnung erstellt.
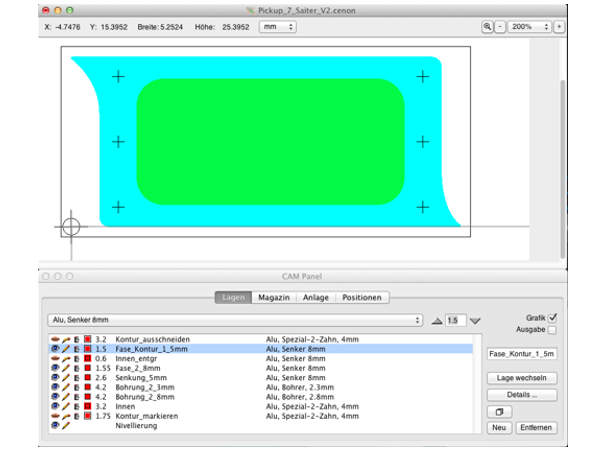
Wenn der Kunde die CAD-Zeichnung freigegeben hat, wird hieraus nun eine für die Fräse lesbare Datei erstellt. Diese Datei enthält zusätzlich die verwendeten Fräser und Parameter wie Drehzahl etc.
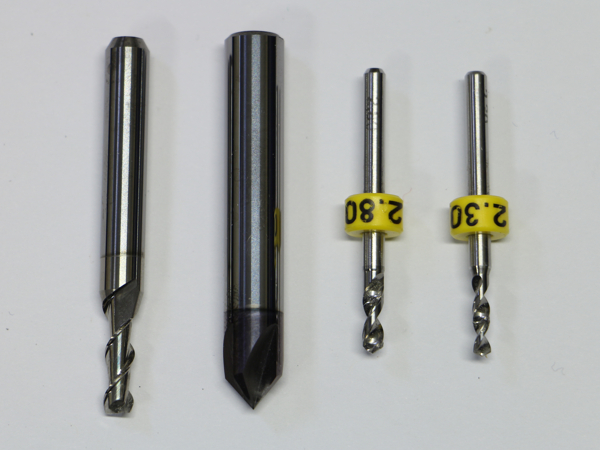
Diese Fräser und Bohrer werden für die Fertigung des Rahmens benötigt. Und obwohl bisher noch gar nichts gefräst wurde, ist schon eine Menge Arbeit erledigt worden.
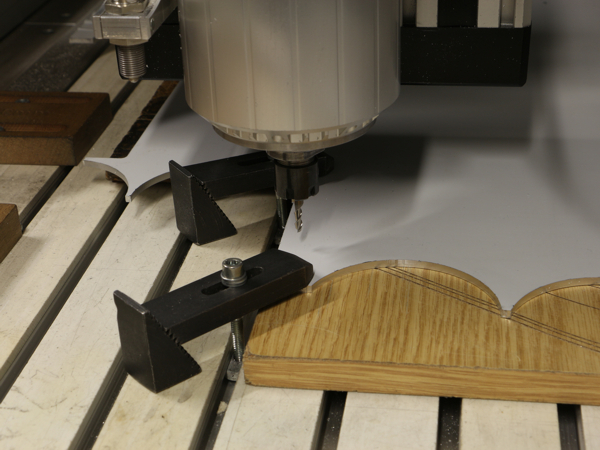
Nun kann es endlich losgehen: Das 4mm starke Aluminium-Blech ist auf der Fräse eingespannt und der Nullpunkt, von dem aus der Rahmen gefräst werden soll, ist festgelegt.
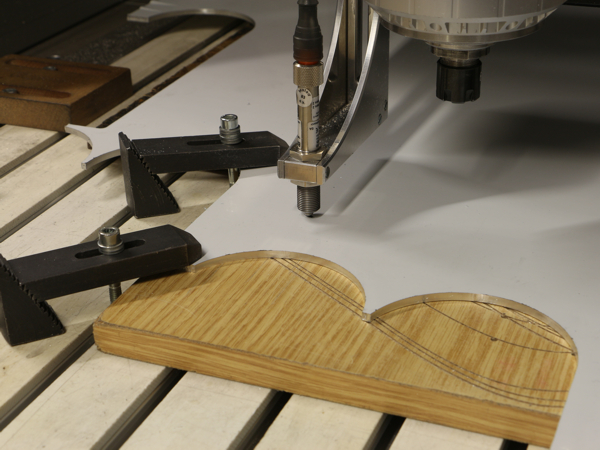
Nun muss zunächst noch die Oberfläche des Aluminiums abgetastet werden. Sollte ein Werkstück uneben sein oder nicht waagerecht auf dem Frästisch aufliegen, so würden Gravuren und Bohrungen unterschiedlich tief werden. Jede Abweichung in der Höhe wird durch diese Messung berücksichtigt und später beim Fräsen ausgeglichen.
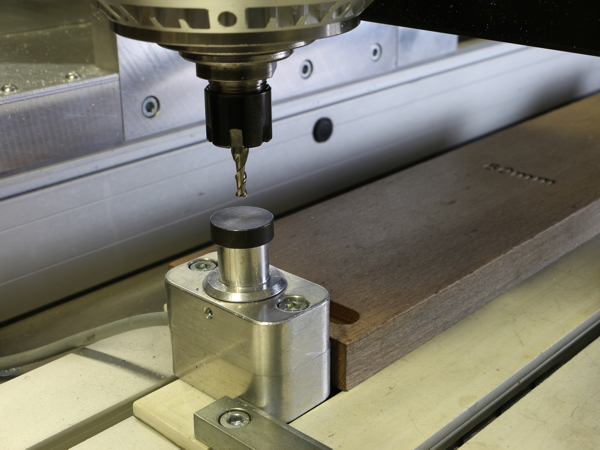
Als nächster Schritt wird die Fräserlänge ausgemessen. So wird bei einem Wechsel des Fräsers immer gleich tief gefräst.
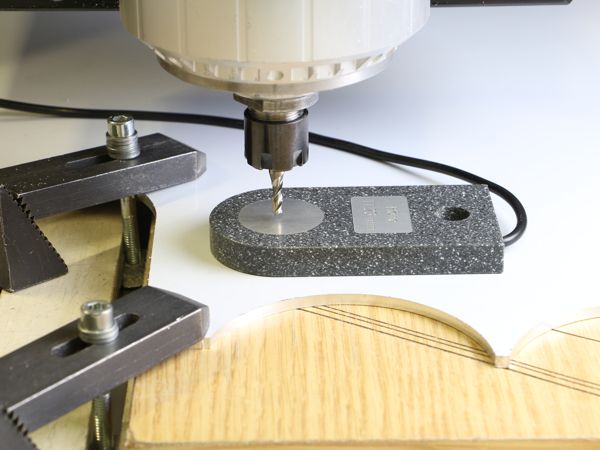
Bevor wir aber fräsen können, muss zunächst erst einmal festgestellt werden, wo sich die Oberfläche des Werkstückes befindet. Nur so werden später Gravuren und Bohrungen mit der korrekten Tiefe ausgeführt.
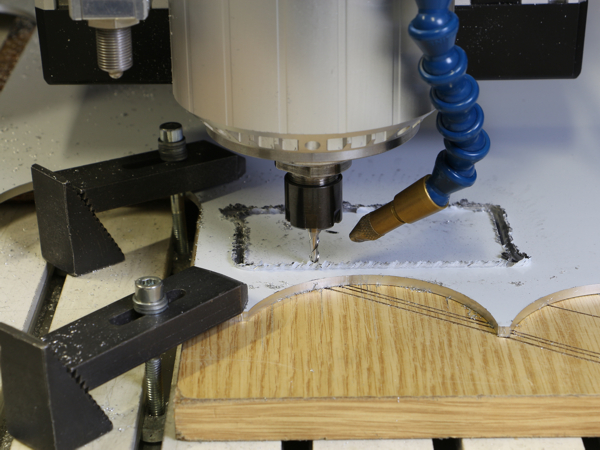
Nach allen Vorbereitungen kann nun endlich die Kontur des Rahmens durch die Schutzfolie hindurch gefräst werden.

Nach dem Entfernen der Schutzfolie muss die Höhe des Werkstückes neu gemessen werden, da die erste Messung durch die Dicke der Folie nicht 100% korrekt war.
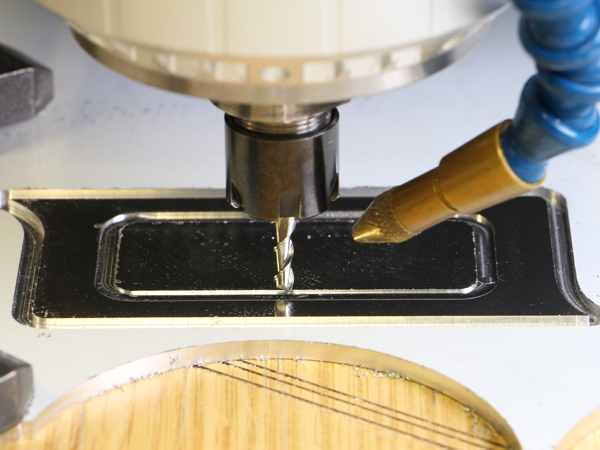
Mit der exakten Werkstückhöhe kann nun die Innenkontur des Rahmens gefräst werden.
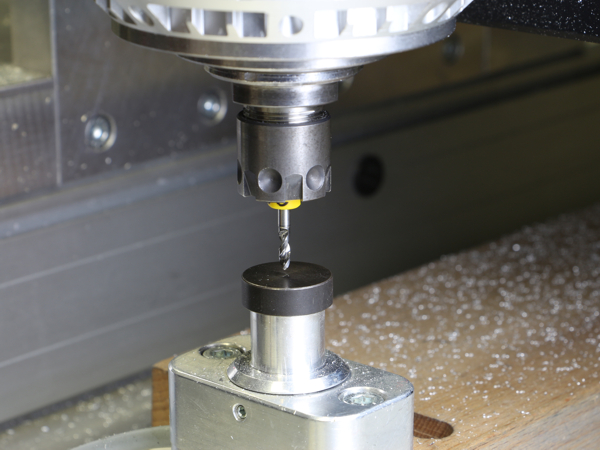
Bevor die Löcher gebohrt werden können, muss die Länge des Bohrers ausgemessen werden.
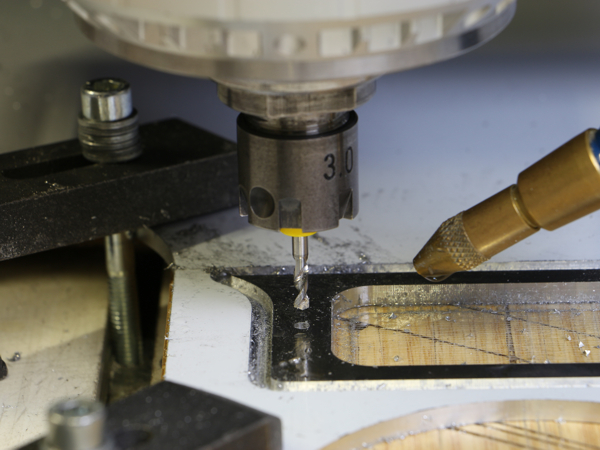
Nun können die Löcher mit der Präzision der CNC-Fräse sehr genau gebohrt werden.
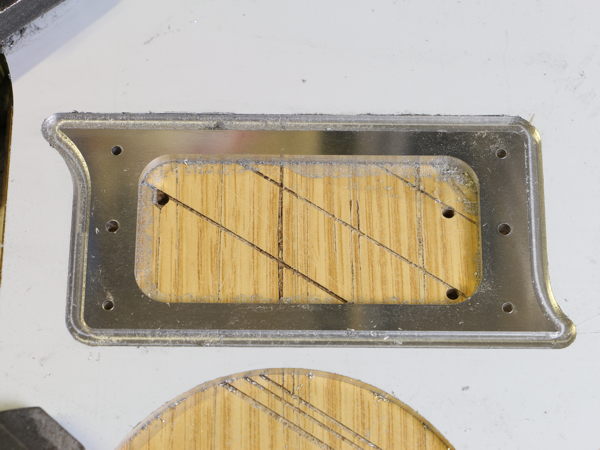
Jetzt ist der Rahmen schon zu erkennen. Allerdings fehlen noch die Senkungen für die Schraubenlöcher und die Kontur hat noch einen starken Grat.
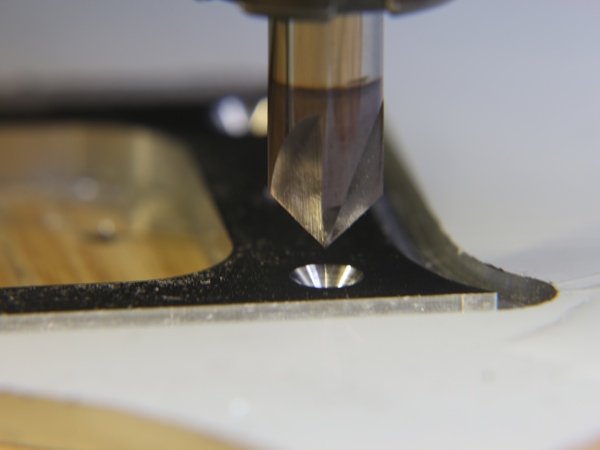
Deshalb kommt nun der Senker zum Einsatz. Nachdem die Länge dieses Werkzeuges zuvor wieder ausgemessen wurde, werden zunächst die Schraubenlöcher bearbeitet...
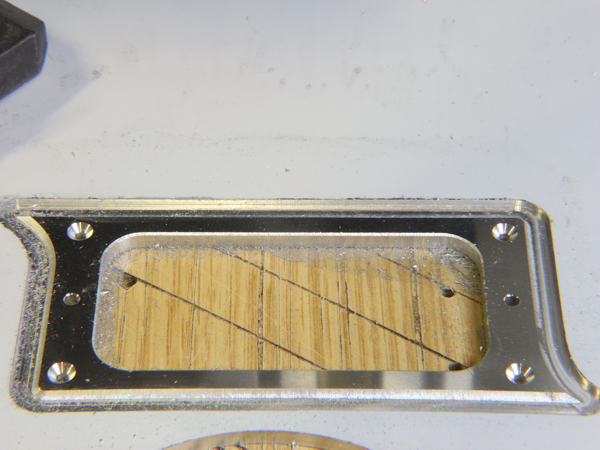
Mit dem gleichen Werkzeug wird die Innenkontur entgratet und die Außenkontur erhält eine starke Fase.
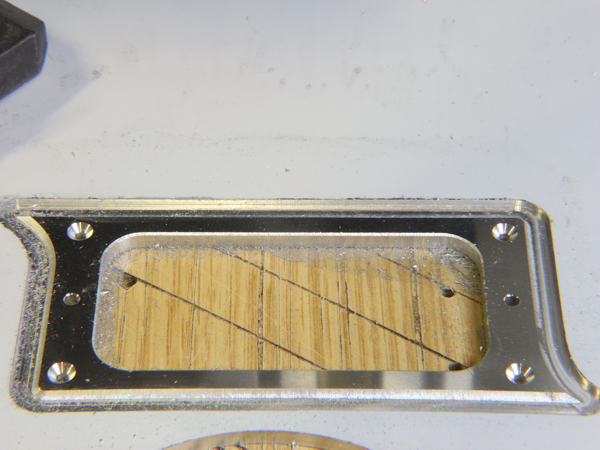
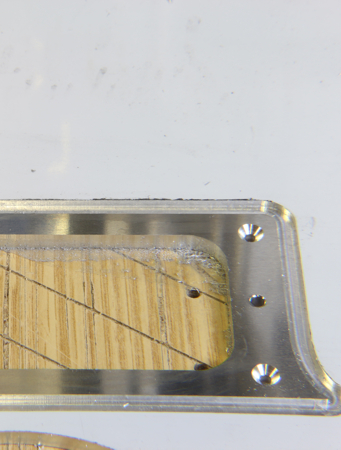
Der Vergleich vor und nach der Bearbeitung mit dem Senker ist doch ziemlich eindrucksvoll.
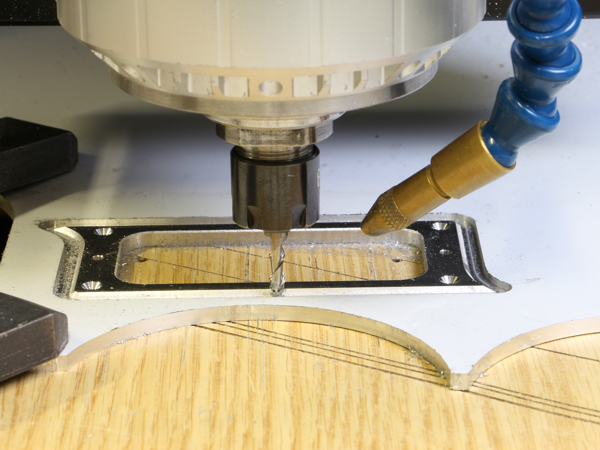
Schließlich kann die Außenkontur komplett ausgefräst werden.
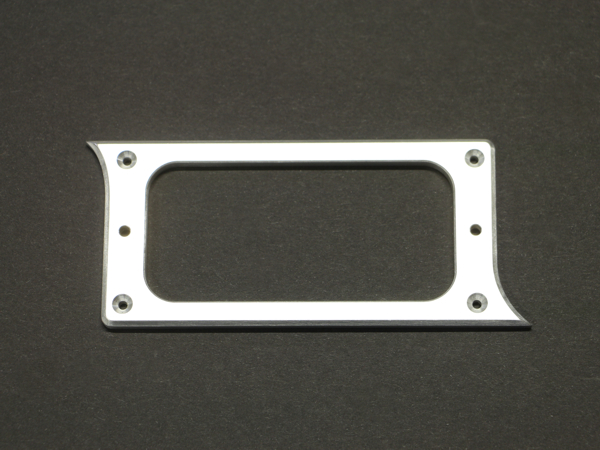
Nach allen diesen Arbeitsschritten ist der gewünschte Rahmen nun endlich fertig. Es müssen jetzt noch mit Schleifpapier die letzten Frässpuren an den Konturen entfernt werden, Die Oberfläche wird in diesem Fall aber vom Kunden weiterbearbeitet.
Fertigung eines Rahmens für einen Tonabnehmer (1/21)
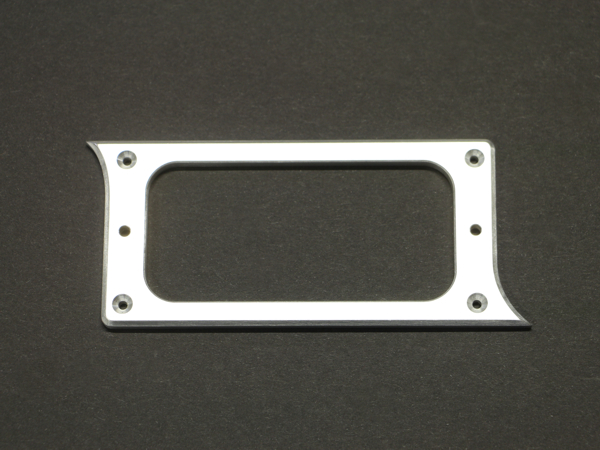
Dieser Rahmen soll für einen Tonabnehmer einer Gitarre gefräst werden.
Fertigung eines Rahmens für einen Tonabnehmer (2/21)
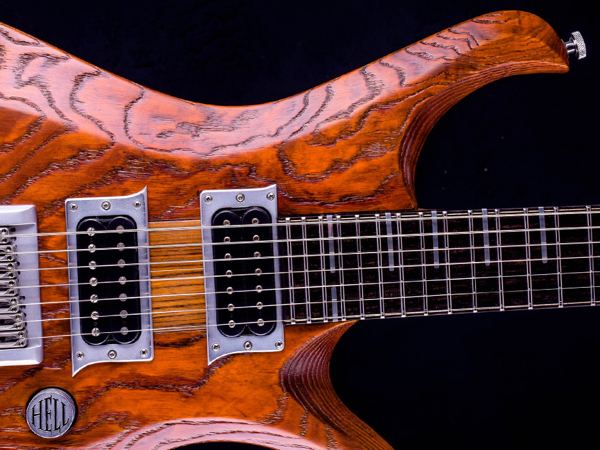
So wird er später einmal mit dem Tonabnehmer auf der Gitarre sitzen.
Fertigung eines Rahmens für einen Tonabnehmer (3/21)
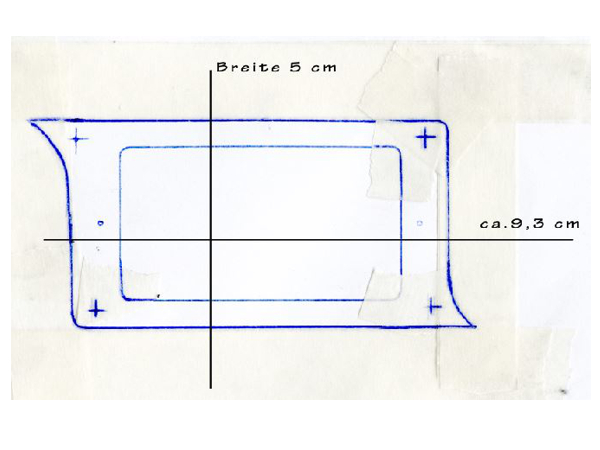
Ausgangspunkt für den Rahmen ist die Zeichnung des Kunden.
Fertigung eines Rahmens für einen Tonabnehmer (4/21)
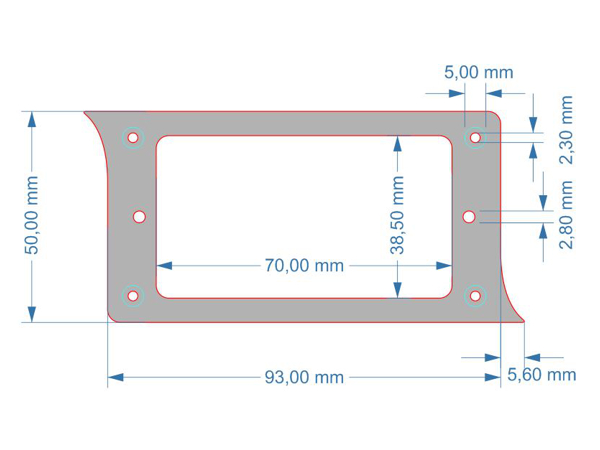
Auf Basis der Kundenzeichnung wird nun in eine bemaßte CAD-Zeichnung erstellt.
Fertigung eines Rahmens für einen Tonabnehmer (5/21)
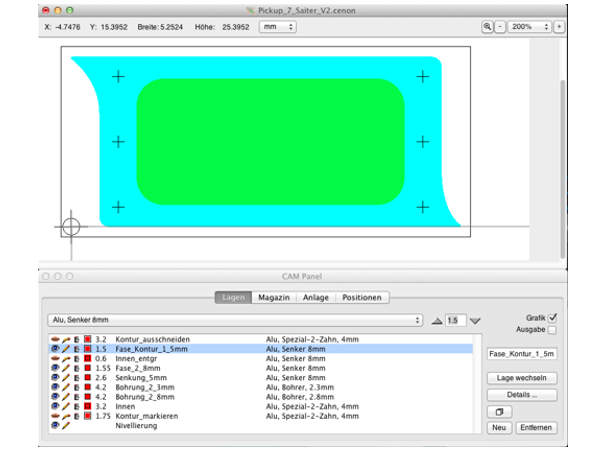
Wenn der Kunde die CAD-Zeichnung freigegeben hat, wird hieraus nun eine für die Fräse lesbare Datei erstellt. Diese Datei enthält zusätzlich die verwendeten Fräser und Parameter wie Drehzahl etc.
Fertigung eines Rahmens für einen Tonabnehmer (6/21)
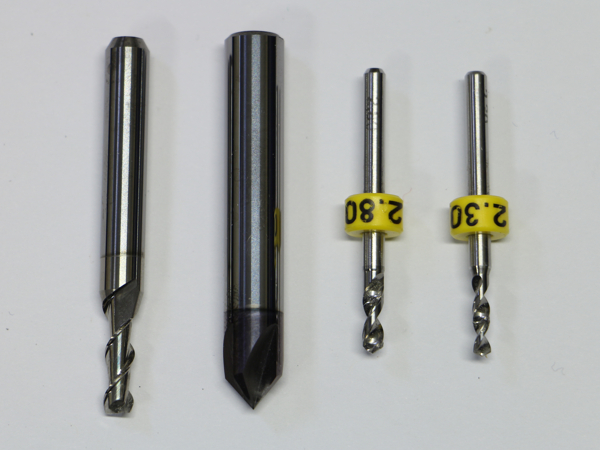
Diese Fräser und Bohrer werden für die Fertigung des Rahmens benötigt. Und obwohl bisher noch gar nichts gefräst wurde, ist schon eine Menge Arbeit erledigt worden.
Fertigung eines Rahmens für einen Tonabnehmer (7/21)
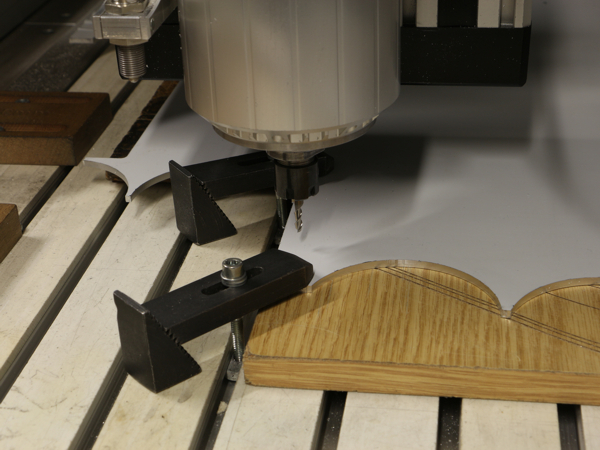
Nun kann es endlich losgehen: Das 4mm starke Aluminium-Blech ist auf der Fräse eingespannt und der Nullpunkt, von dem aus der Rahmen gefräst werden soll, ist festgelegt.
Fertigung eines Rahmens für einen Tonabnehmer (8/21)
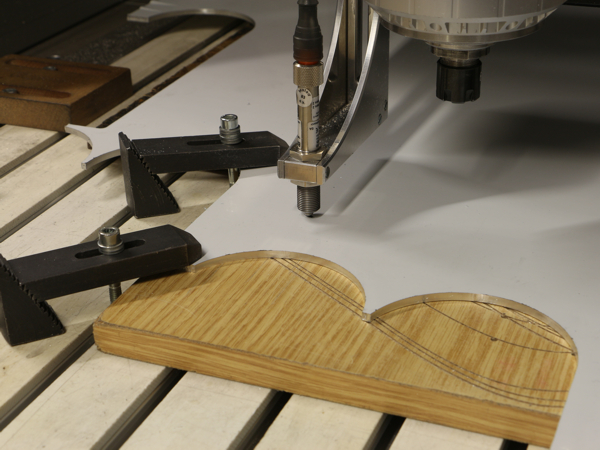
Nun wird die Oberfläche des Aluminiums abgetastet. Sollte ein Werkstück uneben sein oder nicht waagerecht auf dem Frästisch aufliegen, so würden Gravuren und Bohrungen unterschiedlich tief werden. Jede Abweichung in der Höhe wird durch diese Messung berücksichtigt und später ausgeglichen.
Fertigung eines Rahmens für einen Tonabnehmer (9/21)
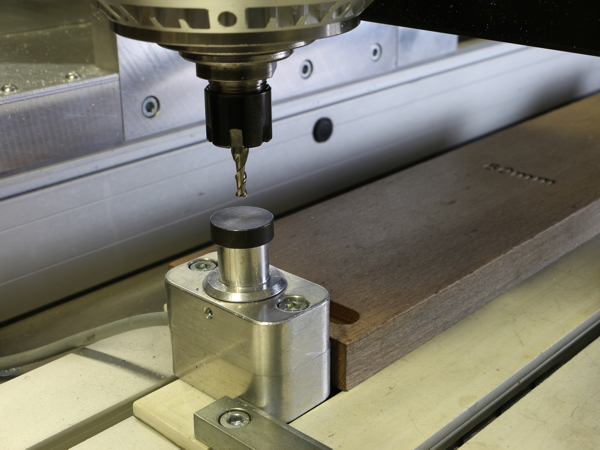
Als nächster Schritt wird die Fräserlänge ausgemessen. So wird bei einem Wechsel des Fräsers immer gleich tief gefräst.
Fertigung eines Rahmens für einen Tonabnehmer (10/21)
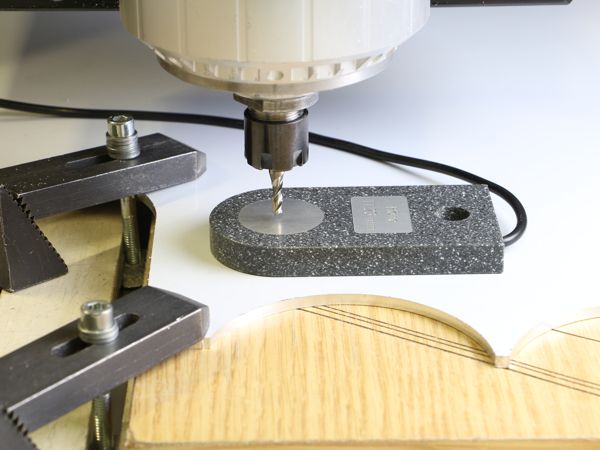
Bevor wir aber fräsen können, muss zunächst erst einmal festgestellt werden, wo sich die Oberfläche des Werkstückes befindet. Nur so werden später Gravuren und Bohrungen mit der korrekten Tiefe ausgeführt.
Fertigung eines Rahmens für einen Tonabnehmer (11/21)
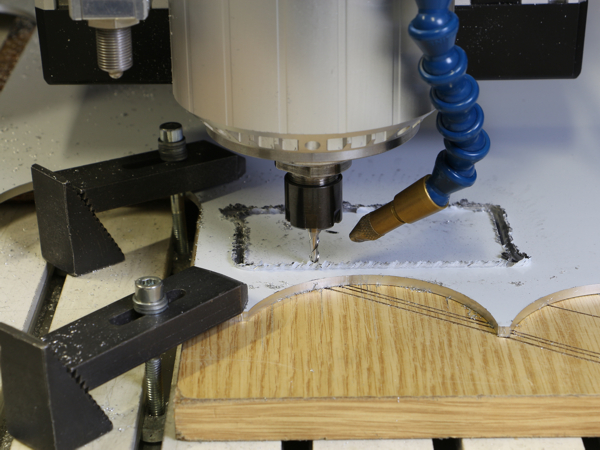
Nach allen Vorbereitungen kann nun endlich die Kontur des Rahmens durch die Schutzfolie hindurch gefräst warden.
Fertigung eines Rahmens für einen Tonabnehmer (12/21)

Nach dem Entfernen der Schutzfolie muss die Höhe des Werkstückes neu gemessen werden, da die erste Messung durch die Dicke der Folie nicht 100% korrekt war.
Fertigung eines Rahmens für einen Tonabnehmer (13/21)
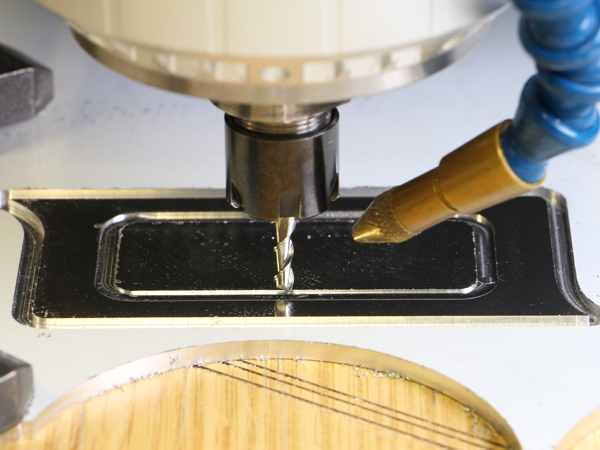
Mit der exakten Werkstückhöhe kann nun die Innenkontur des Rahmens gefräst warden.
Fertigung eines Rahmens für einen Tonabnehmer (14/21)
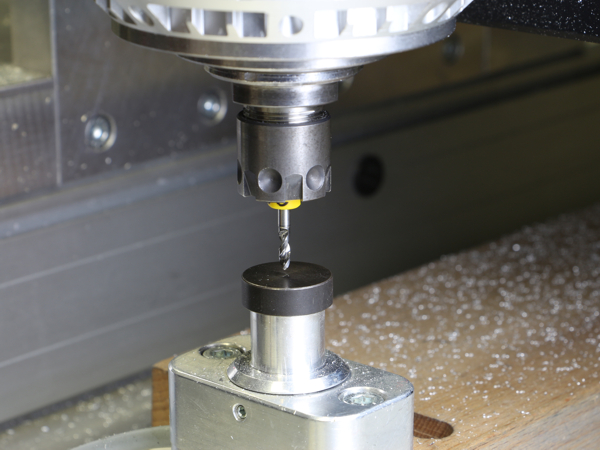
Bevor die Löcher gebohrt werden können, muss die Länge des Bohrers ausgemessen werden
Fertigung eines Rahmens für einen Tonabnehmer (15/21)
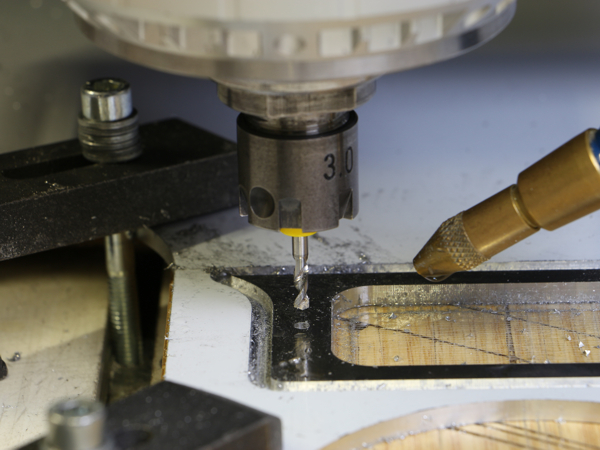
Nun können die Löcher mit der Präzision der CNC-Fräse sehr genau gebohrt warden.
Fertigung eines Rahmens für einen Tonabnehmer (16/21)
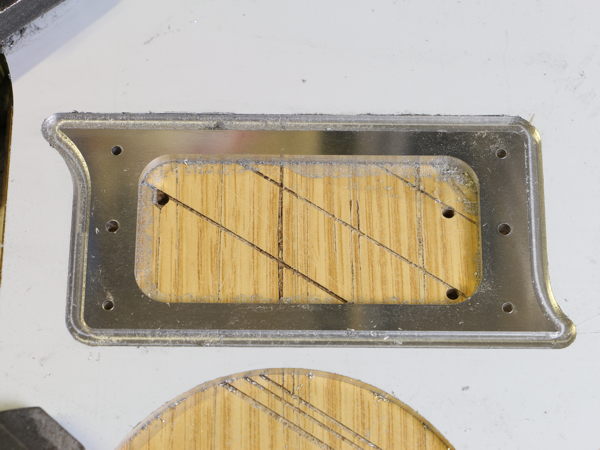
Jetzt ist der Rahmen schon zu erkennen. Allerdings fehlen noch die Senkungen für die Schraubenlöcher und die Kontur hat noch einen starken Grat.
Fertigung eines Rahmens für einen Tonabnehmer (17/21)
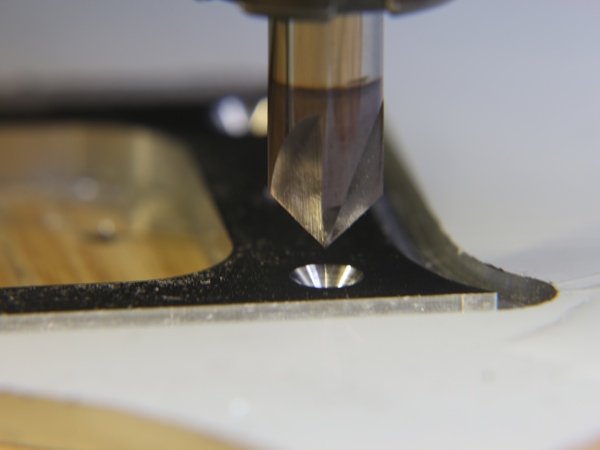
Deshalb kommt nun der Senker zum Einsatz. Nachdem die Länge dieses Werkzeuges zuvor wieder ausgemessen wurde, werden zunächst die Schraubenlöcher bearbeitet...
Fertigung eines Rahmens für einen Tonabnehmer (18/21)
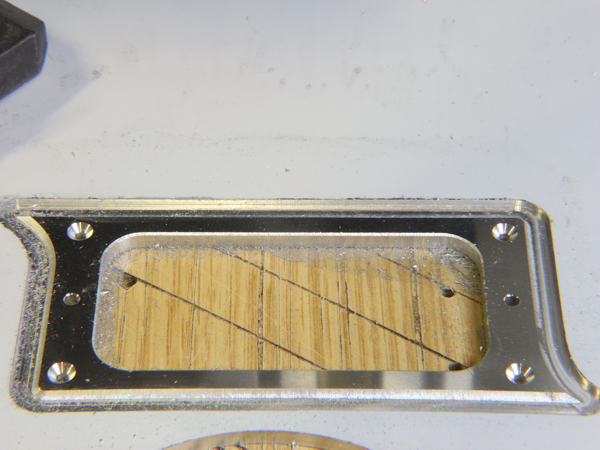
Mit dem gleichen Werkzeug wird die Innenkontur entgratet und die Außenkontur erhält eine starke Fase.
Fertigung eines Rahmens für einen Tonabnehmer (19/21)
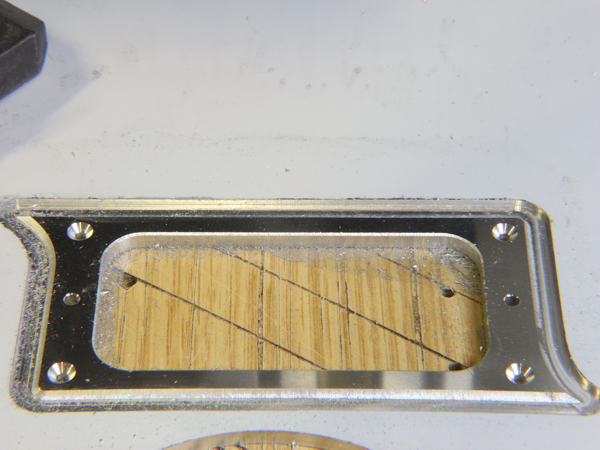
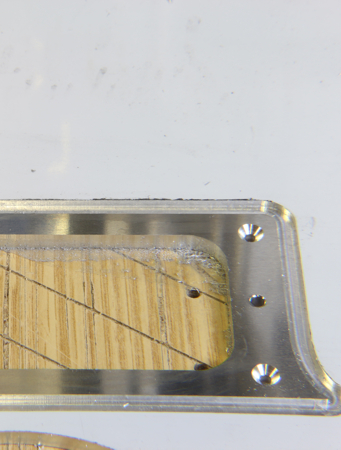
Der Vergleich vor und nach der Bearbeitung mit dem Senker ist doch ziemlich eindrucksvoll.
Fertigung eines Rahmens für einen Tonabnehmer (20/21)
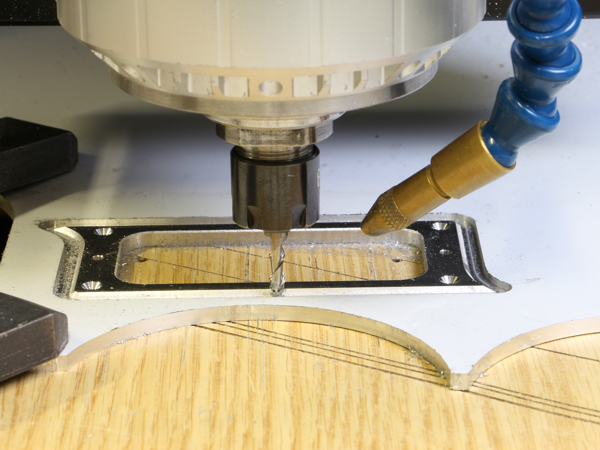
Schließlich kann die Außenkontur komplett ausgefräst werden.
Fertigung eines Rahmens für einen Tonabnehmer (21/21)
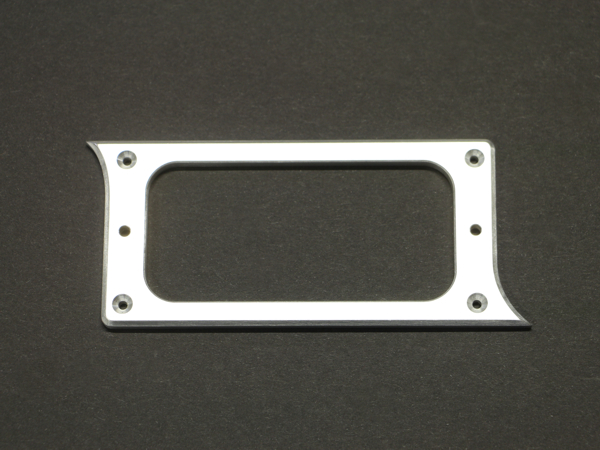
Nach allen diesen Arbeitsschritten ist der gewünschte Rahmen nun endlich fertig. Es müssen jetzt noch mit Schleifpapier die letzten Frässpuren an den Konturen entfernt werden, Die Oberfläche wird in diesem Fall aber vom Kunden weiterbearbeitet.
Fertigung eines Kugelschreibers aus verschiedenen Hölzern
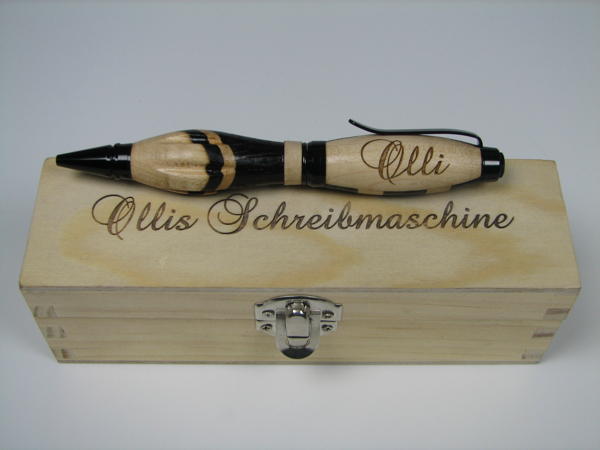
Olli soll einen Kugelschreiber aus Wenge und Ahorn bekommen.
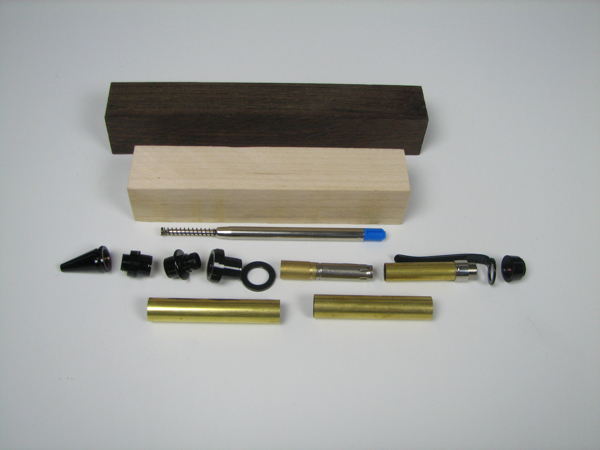
Die Zutaten für den Schreiber sind 2 Kanteln Holz (1x Wenge, 1 x Ahorn) und die Drehmachanik des Kulies. Dies ist der Stoff, aus dem man Kugelschreiber macht.
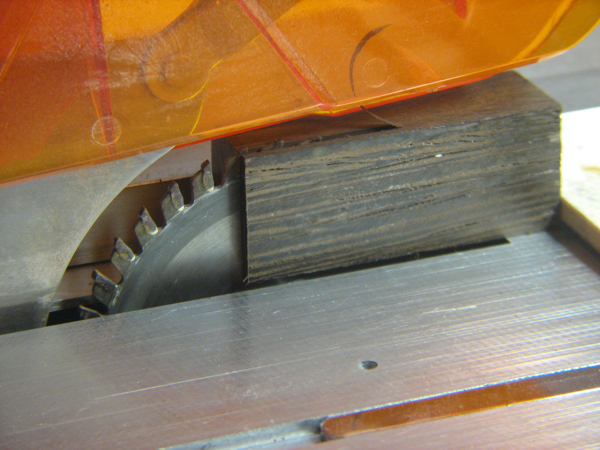
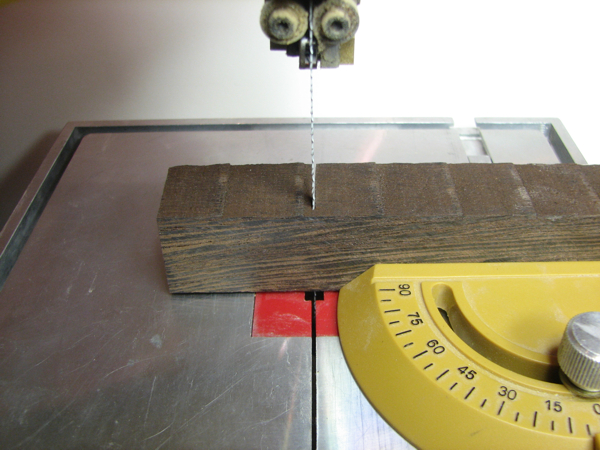
Zuerst muss das Holz zurechtgeschnitten werden. Der Zuschnitt erfolgt je nach Erfordernis mit der Bandsäge oder mit der Kreissäge
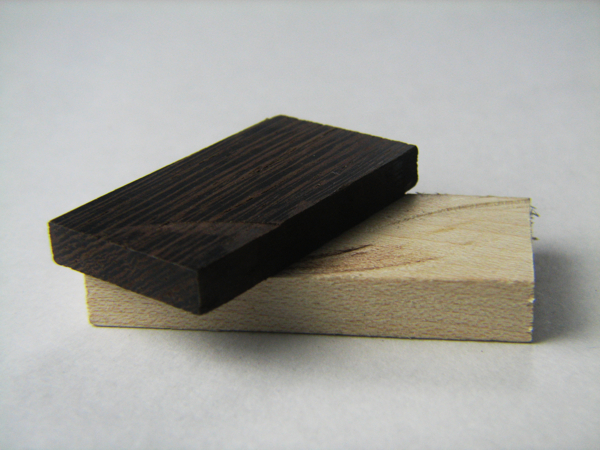
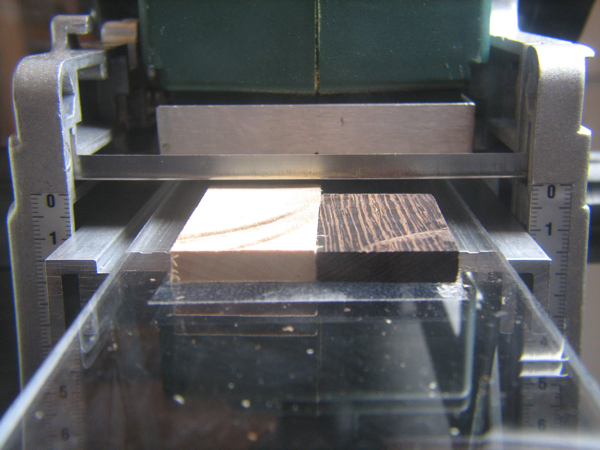
Beim Sägen verbleiben jedoch meistens kleinere Unebenheiten. Deshalb werden die Hölzer mit einem Abrichthobel geglättet. In diesen Fall sorgt das auch gleich dafür, dass beide Hölzer exakt die gleiche Höhe haben.
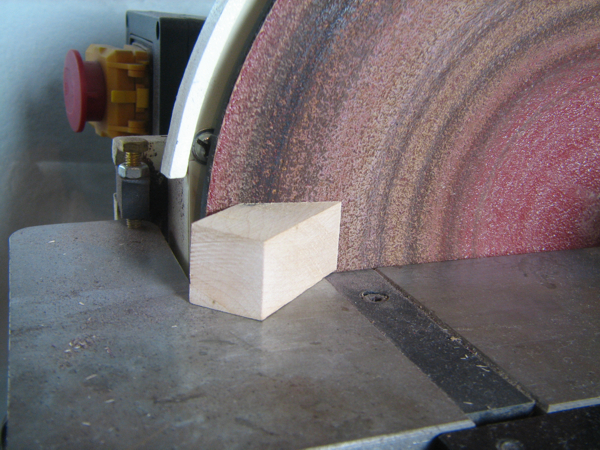
Bauteile, die aus geometrischen Gründen nicht mit dem Abrichthobel bearbeitet werden können, werden entweder an der Schleifmaschine oder auch von Hand geschliffen.
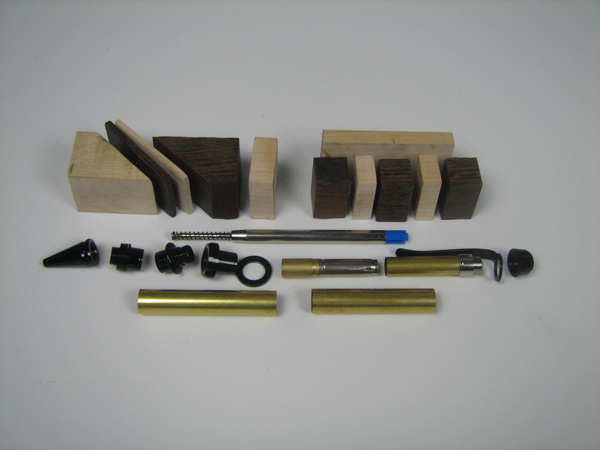
Nach diesen Arbeitsschritten sieht der Kugelschreiber wie hier gezeigt aus.
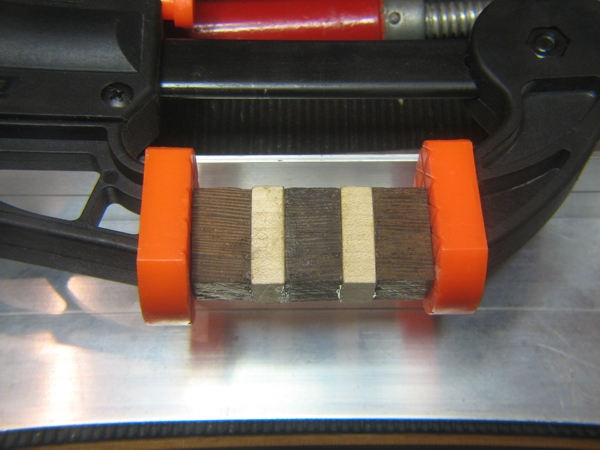
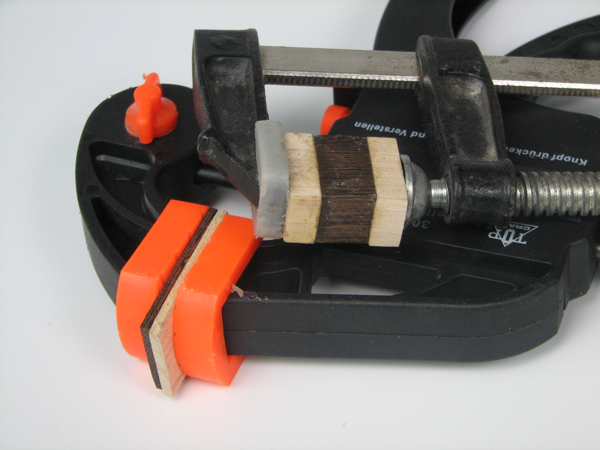
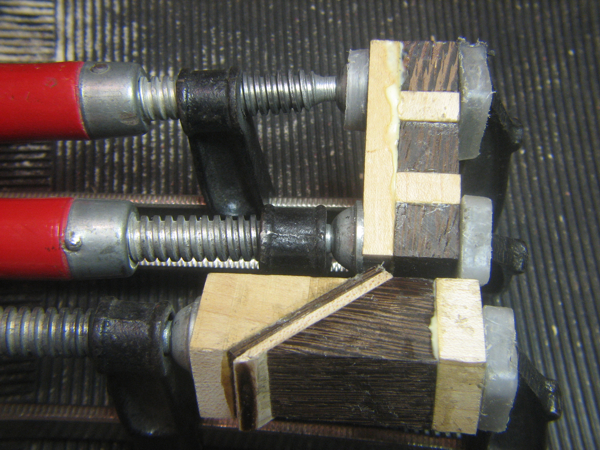
Als nächster Schritt folgt jetzt das Zusammenleimen der Holzteile.
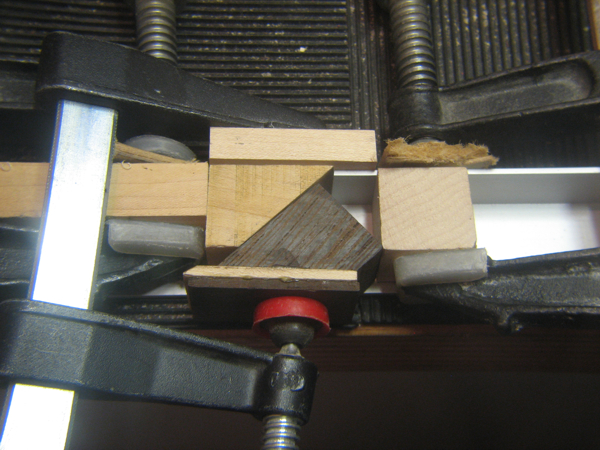
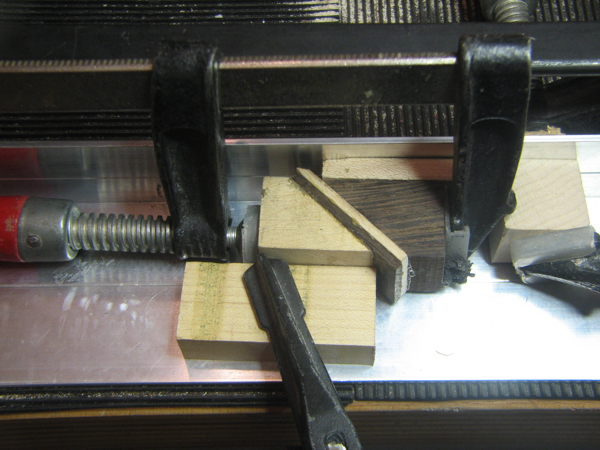
Hierbei ist es teilweise notwendig, sehr kreativ eigene Hilfskonstruktionen zu entwickeln.
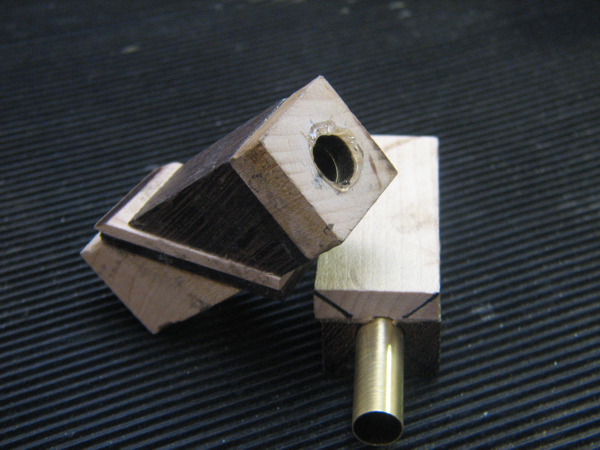
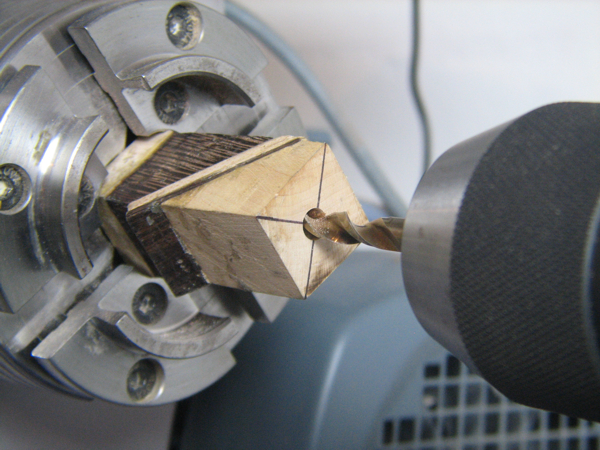
Jetzt müssen die Löcher für die Hülsen gebohrt werden, die später die Kugelschreibermine führen. Im linken Holzblock des rechten Bildes ist die Hülse schon eingeklebt.
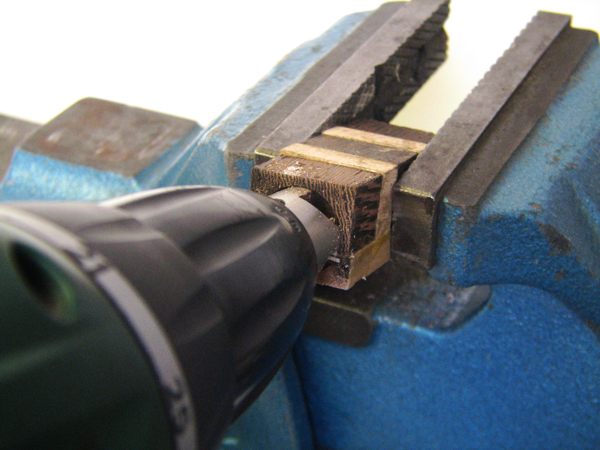
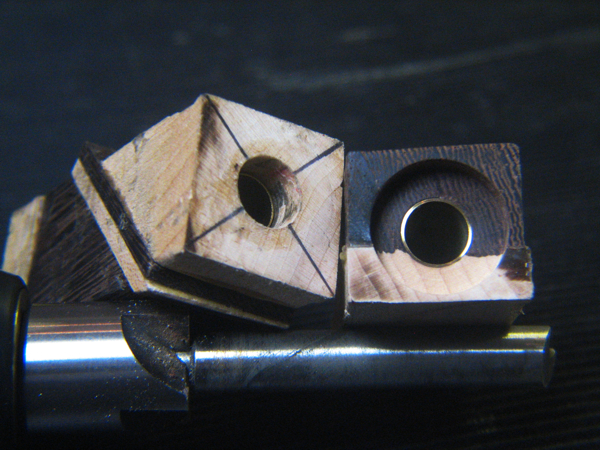
Nun werden die Stirnseiten rechtwinklig gefräst und der Block auf die entgültige Länge gebracht. Das rechte Bild zeigt die Blöcke vor und nach diesem Arbeitsschritt. Auch die eingeklebte Messinghülse ist gut zu erkennen.
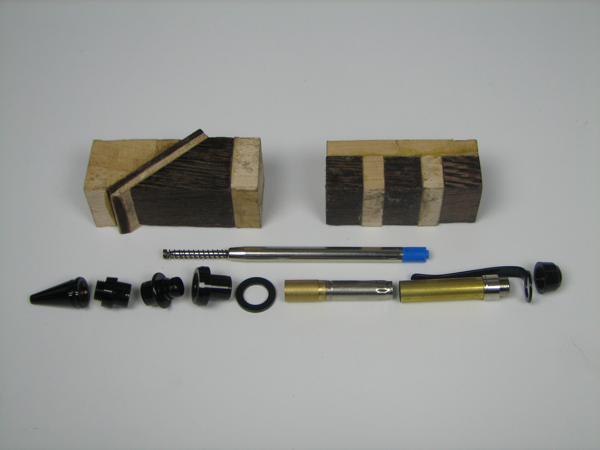
Nach diesen Arbeitsschritten sieht der Kugelschreiber wie hier gezeigt aus.
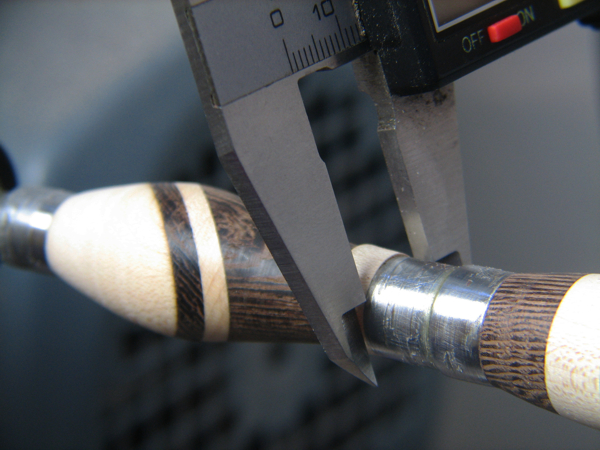
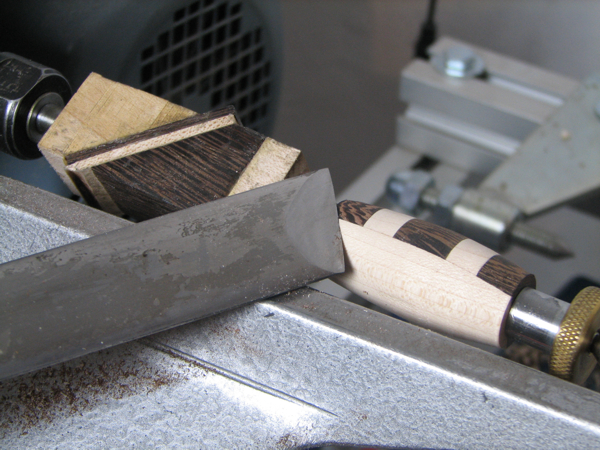
Nun kommt endlich das Eckige ins Runde: Die Kontur des Kulies wird gedrechselt und der linke viereckige Block erhält seine runde Form. Die Durchmesser der nun runden Hölzer müssen später exakt zur Drehmechanik passen. Also besser noch mal messen.
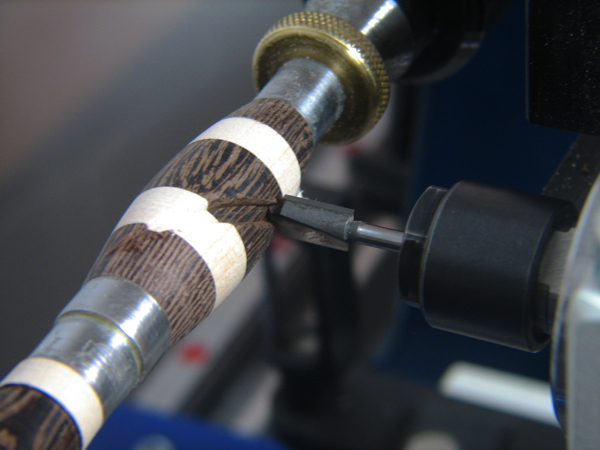
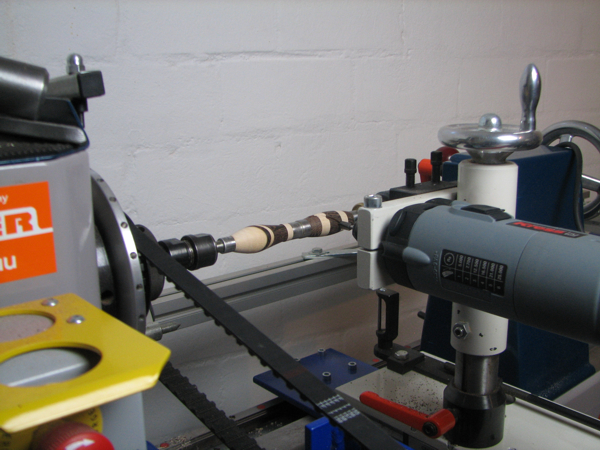
Der hintere Teil des Kulies soll eine Spiralnut erhalten. Hierzu wird die Kanneliereinheit in Verbindung mit einem Viertelkreisfräser eingesetzt. So entsteht eine sehr exakte Spiralnut.
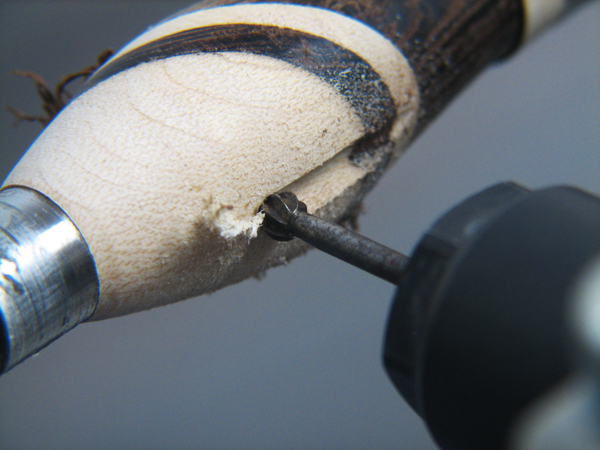
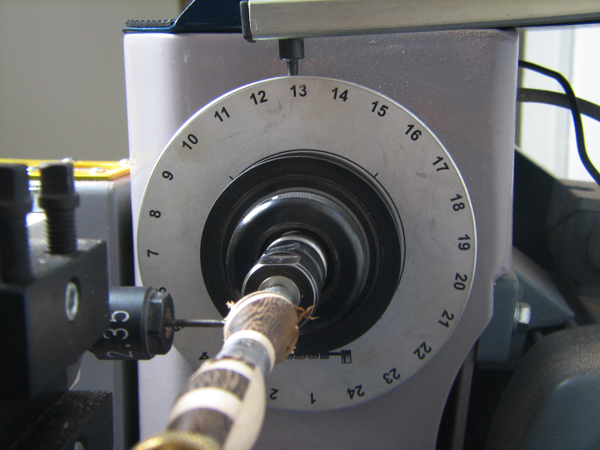
Im nächsten Arbeitsschritt soll das Griffstück des Kulies gerade Nuten bekommen. Dazu wird ein Kugelfräser mit einer Teilscheibe verwendet. Damit können die Nuten in immer gleichen Abständen angebracht werden und werden so absolut gleichmäßig auf dem Umfang des Schreibers verteilt.
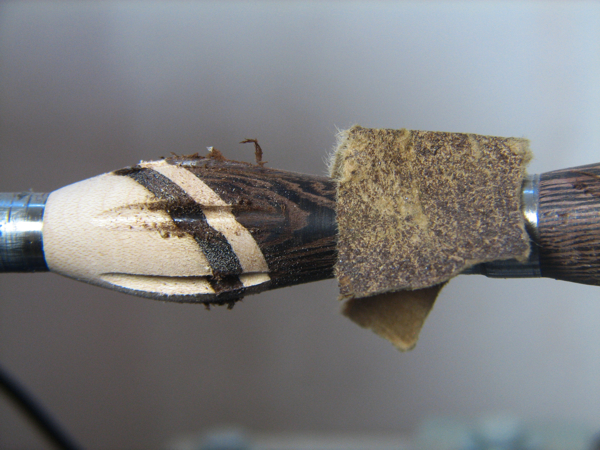
Um die letzten Spuren des Fräsens und des Drechselns zu beseitigen, muss nun der gesamte Kuli mit Schmirgelpapier verschiedener Körnung geglättet werden. Dies geschieht ganz normal in Handarbeit.
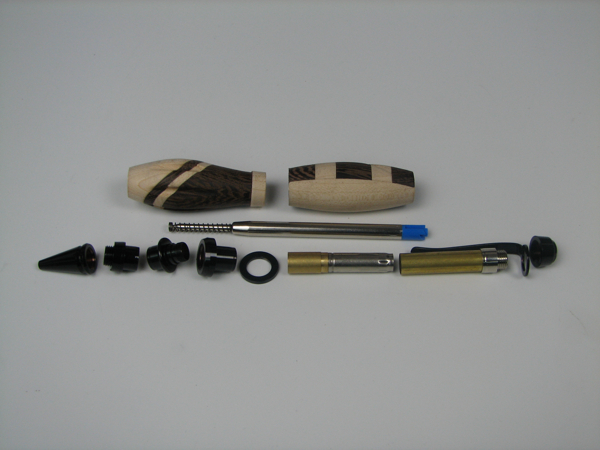
Nach diesen Arbeitsschritten sieht der Kugelschreiber wie hier gezeigt aus.
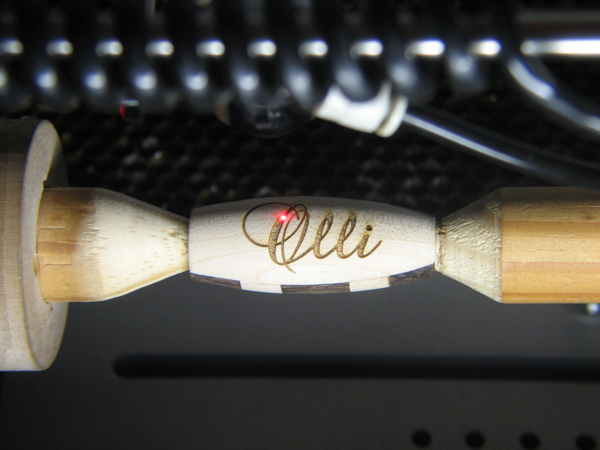
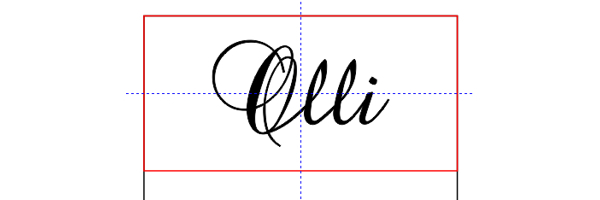
Nun soll der Schreiber noch eine Lasergravur erhalten. Dafür wird zunächst eine Laser-Datei erstellt, die die Schrift über den Umfang des Schreibers abrollt. Dieser Entwurf wird dann im Laser mit einer Abrollvorrichtung ausgeführt.
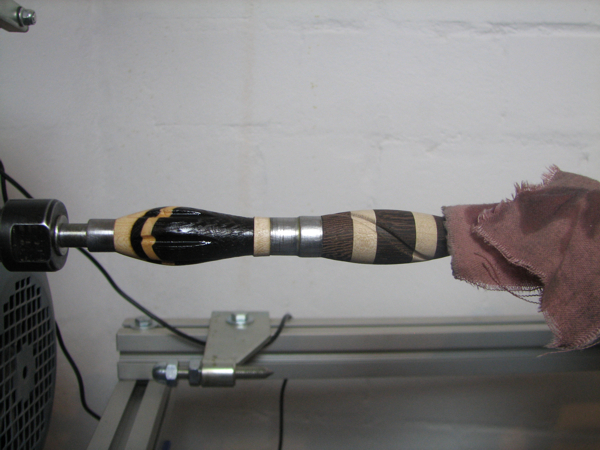
Nachdem die Schmauchspuren des Laserns um die Buchstaben wieder von Hand weggeschmirgelt wurden, wird jetzt eine Oberflächenversiegelung in mehreren Schichten aufgebracht. Der Unterschied zum rohen Holz ist bereits nach der ersten Schicht nicht zu übersehen. Damit ist der Schreiber später gegen Schmutz und Handschweiß beim Schreiben gut geschützt.
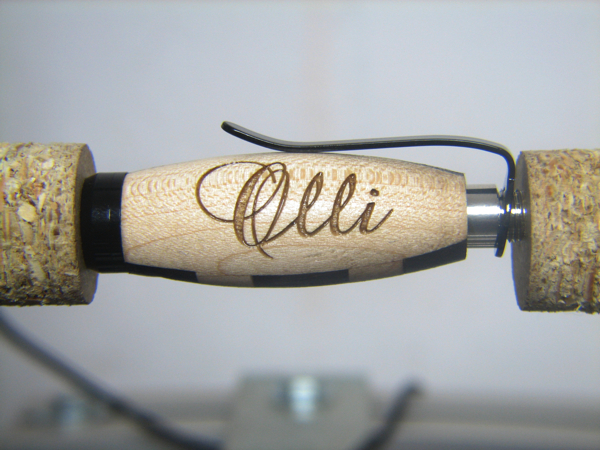
Nun kommt Olli mächtig unter Druck. Das bedeutet, dass die Kugelschreiber-Mechanik jetzt auf bzw. in die Holzteile gepresst wird. Diese Verbindung ist so stark, dass nicht geklebt werden muss.
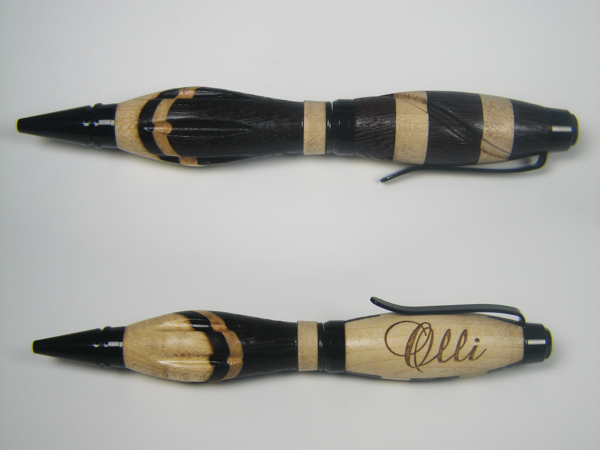
Nach diesen letzten Arbeitsschritten ist der Kuli nun zusammengebaut, damit fertig und bietet als Unikat eine buchstäblich "einmalige" Vorder- und Rückseite.
Fertigung eines Kugelschreibers (1/27)
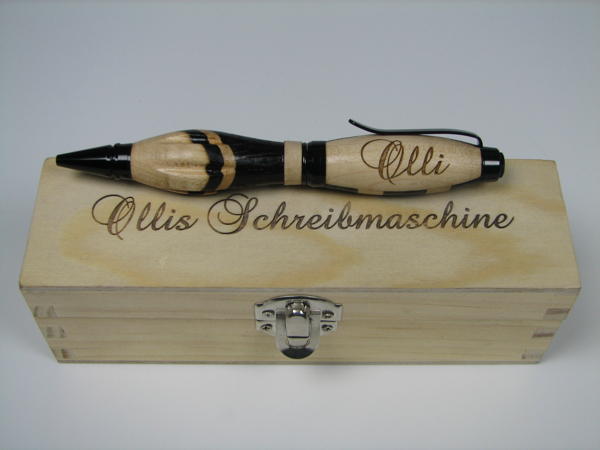
Olli soll einen Kugelschreiber aus Wenge und Ahorn bekommen.
Fertigung eines Kugelschreibers (2/27)
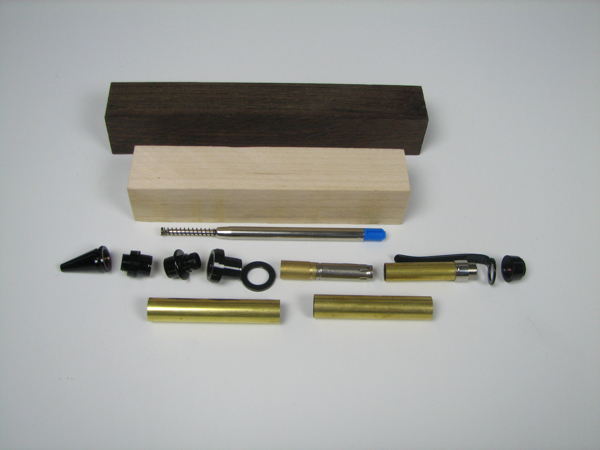
Die Zutaten für den Schreiber sind 2 Kanteln Holz (1x Wenge, 1 x Ahorn) und die Drehmachanik des Kulies. Dies ist der Stoff, aus dem man Kugelschreiber macht.
Fertigung eines Kugelschreibers (3/27)
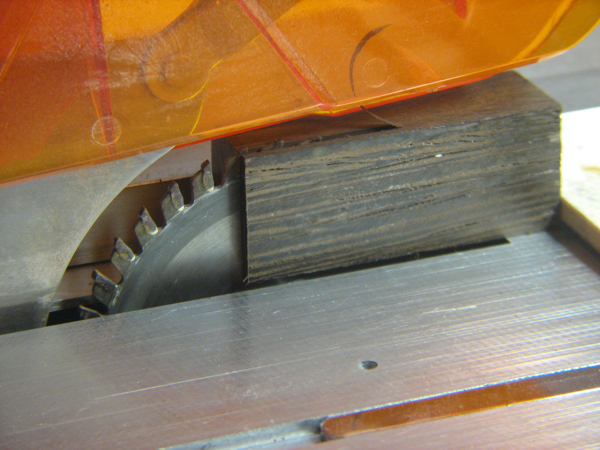
Zuerst muss das Holz zurechtgeschnitten werden. Der Zuschnitt erfolgt je nach Erfordernis mit der Kreissäge oder ...
Fertigung eines Kugelschreibers (4/27)
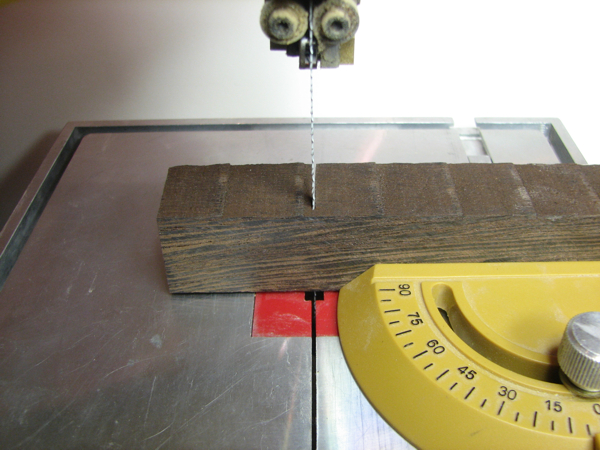
... der Bandsäge.
Fertigung eines Kugelschreibers (5/27)
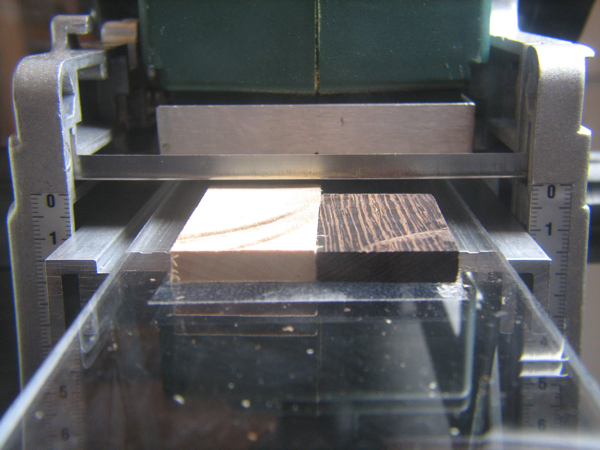
Beim Sägen verbleiben jedoch meistens kleinere Unebenheiten. Deshalb werden die Hölzer mit einem Abrichthobel geglättet. In diesen Fall sorgt das auch gleich dafür, dass beide Hölzer exakt die gleiche Höhe haben.
Fertigung eines Kugelschreibers (6/27)
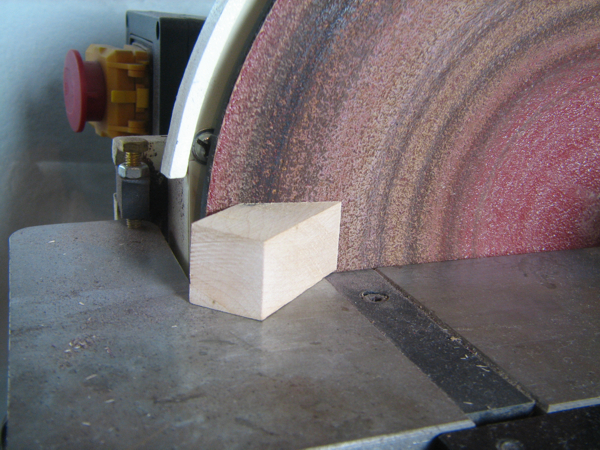
Bauteile, die aus geometrischen Gründen nicht mit dem Abrichthobel bearbeitet werden können, werden entweder an der Schleifmaschine oder auch von Hand geschliffen.
Fertigung eines Kugelschreibers (7/27)
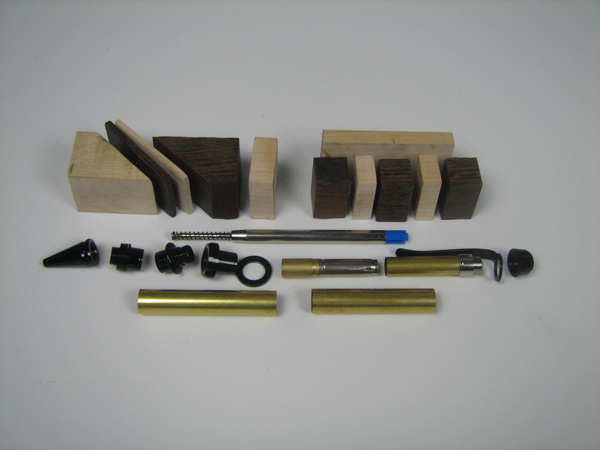
Nach diesen Arbeitsschritten sieht der Kugelschreiber wie hier gezeigt aus.
Fertigung eines Kugelschreibers (8/27)
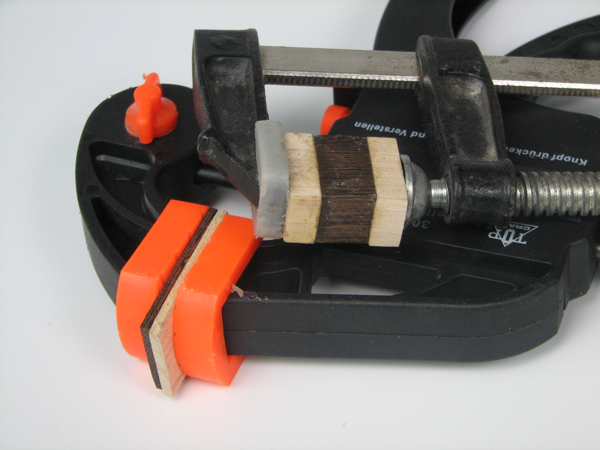
Als nächster Schritt folgt jetzt das Zusammenleimen der Holzteile.
Fertigung eines Kugelschreibers (9/27)
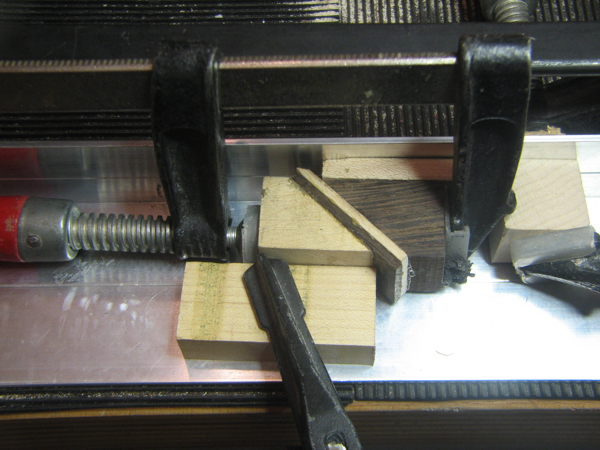
Hierbei ist es teilweise notwendig, sehr kreativ eigene Hilfskonstruktionen zu entwickeln.
Fertigung eines Kugelschreibers (10/27)
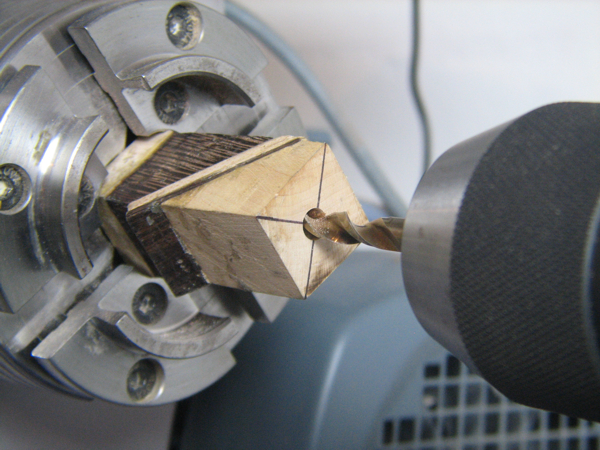
Jetzt müssen die Löcher für die Hülsen gebohrt werden, die später die Kugelschreibermine führen.
Fertigung eines Kugelschreibers (11/27)
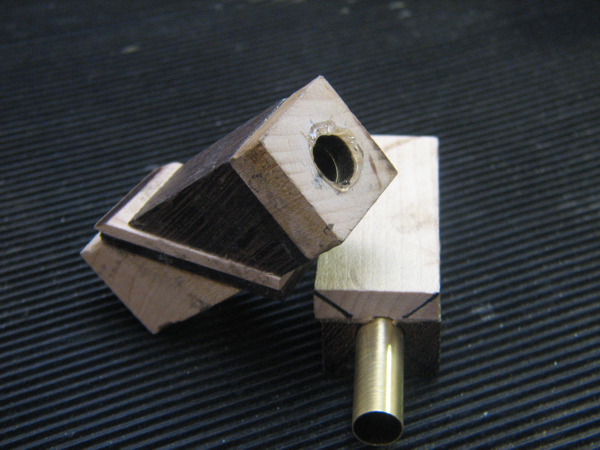
Im linken Holzblock ist die Hülse schon eingeklebt.
Fertigung eines Kugelschreibers (12/27)
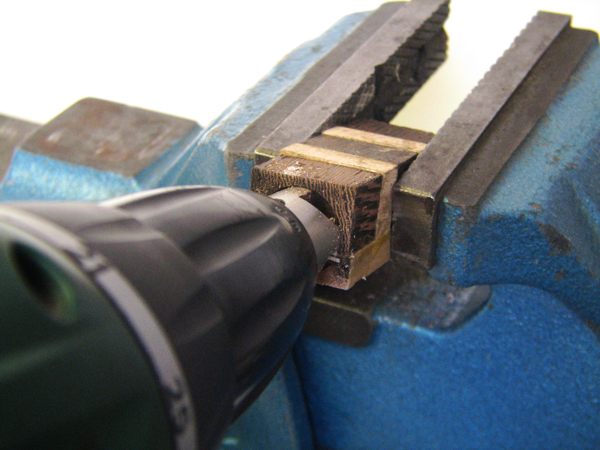
Nun werden die Stirnseiten rechtwinklig gefräst und der Block auf die entgültige Länge gebracht.
Fertigung eines Kugelschreibers (13/27)
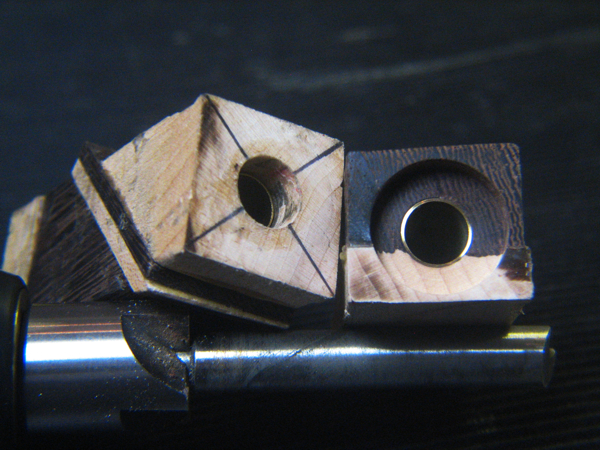
Ein Blick auf die Blöcke vor und nach diesem Arbeitsschritt. Auch die eingeklebte Messinghülse ist gut zu erkennen.
Fertigung eines Kugelschreibers (14/27)
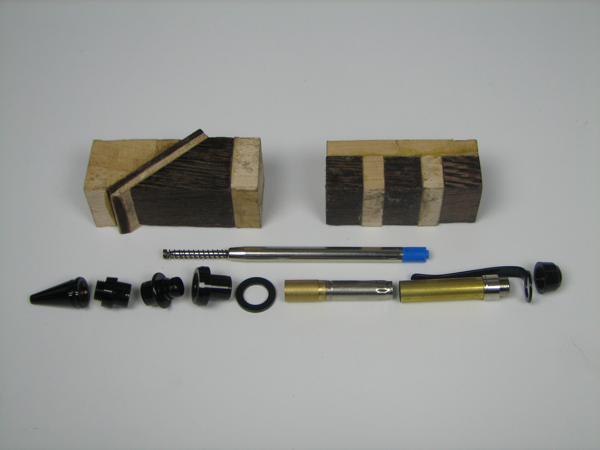
Nach diesen Arbeitsschritten sieht der Kugelschreiber wie hier gezeigt aus.
Fertigung eines Kugelschreibers (15/27)
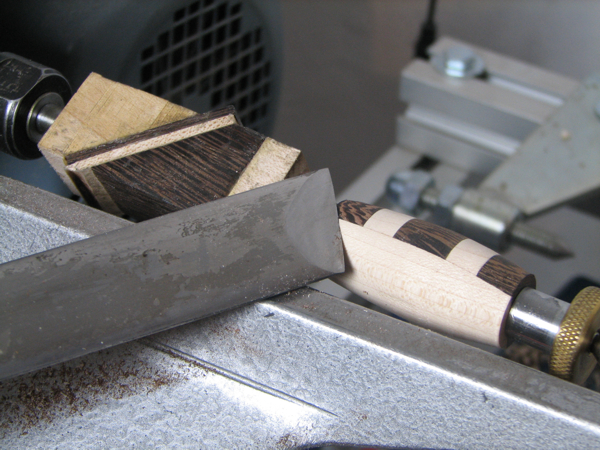
Nun kommt endlich das Eckige ins Runde: Die Kontur des Kulies wird gedrechselt und der linke viereckige Block erhält seine runde Form.
Fertigung eines Kugelschreibers (16/27)
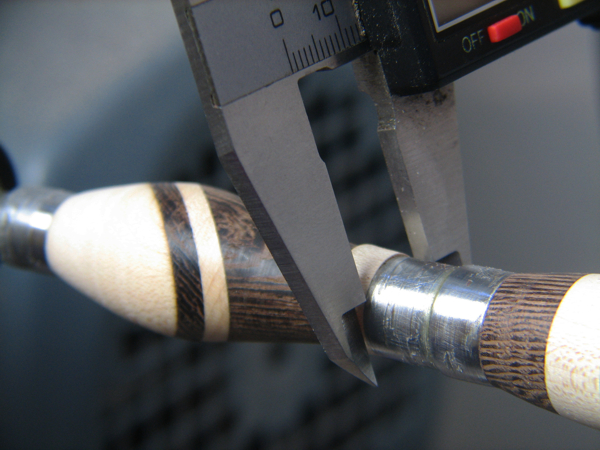
Die Durchmesser der nun runden Hölzer müssen später exakt zur Drehmechanik passen. Also besser noch mal messen.
Fertigung eines Kugelschreibers (17/27)
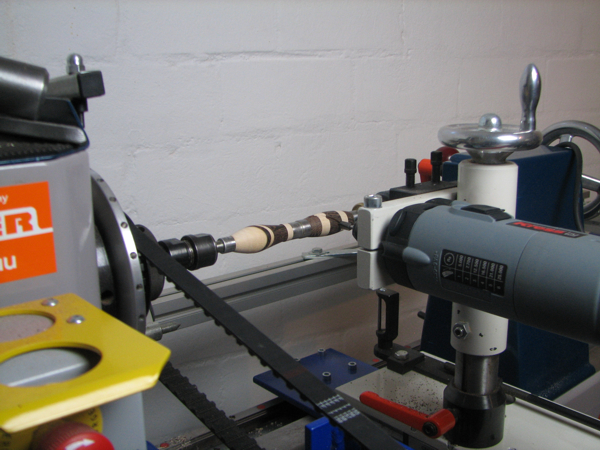
Der hintere Teil des Kulies soll eine Spiralnut erhalten. Hierzu wird die Kanneliereinheit in Verbindung mit einem Viertelkreisfräser eingesetzt
Fertigung eines Kugelschreibers (18/27)
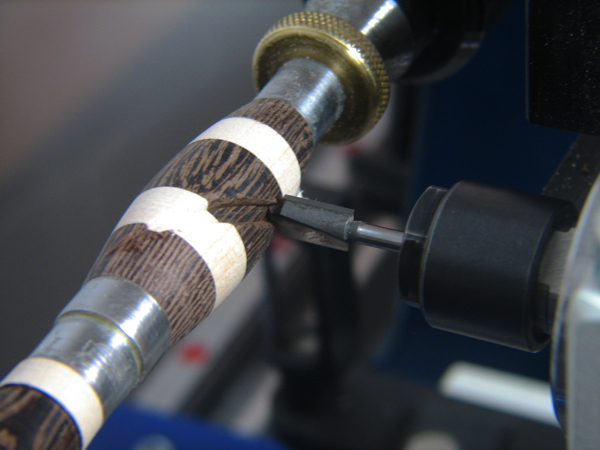
So entsteht eine sehr exakte Spiralnut.
Fertigung eines Kugelschreibers (19/27)
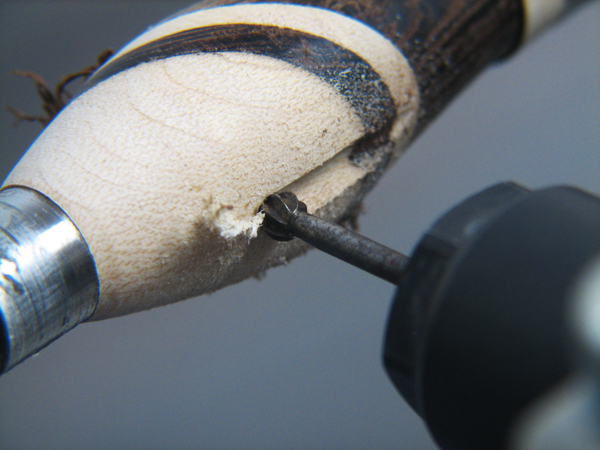
Im nächsten Arbeitsschritt soll das Griffstück des Kulies gerade Nuten bekommen. Dazu wird ein Kugelfräser mit einer Teilscheibe verwendet.
Fertigung eines Kugelschreibers (20/27)
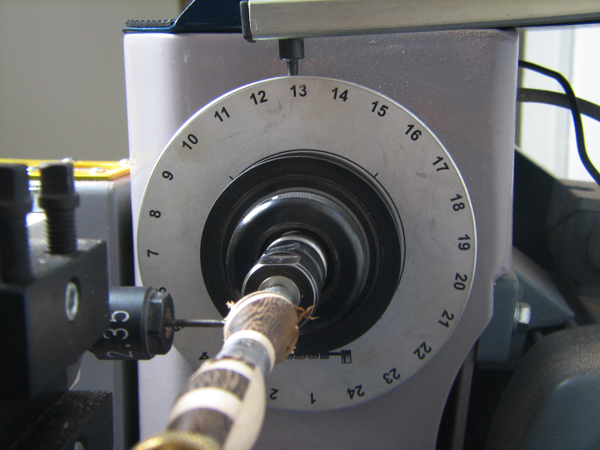
Damit können die Nuten in immer gleichen Abständen angebracht werden und werden so absolut gleichmäßig auf dem Umfang des Schreibers verteilt.
Fertigung eines Kugelschreibers (21/27)
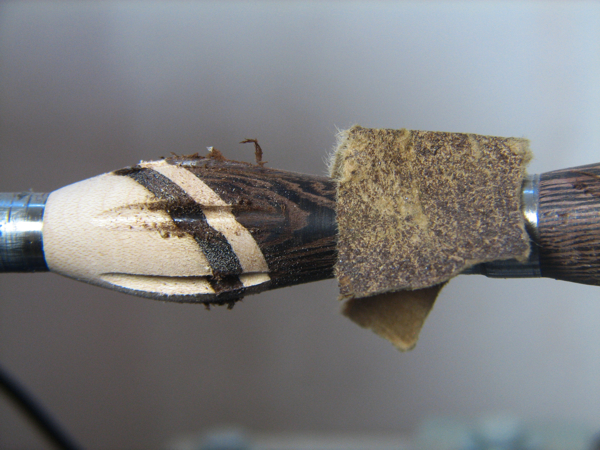
Um die letzten Spuren des Fräsens und des Drechselns zu beseitigen, muss nun der gesamte Kuli mit Schmirgelpapier verschiedener Körnung geglättet werden. Dies geschieht ganz normal in Handarbeit.
Fertigung eines Kugelschreibers (22/27)
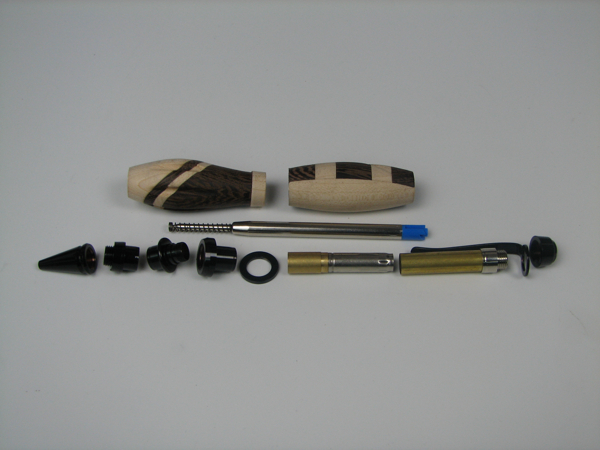
Nach diesen Arbeitsschritten sieht der Kugelschreiber wie hier gezeigt aus.
Fertigung eines Kugelschreibers (23/27)
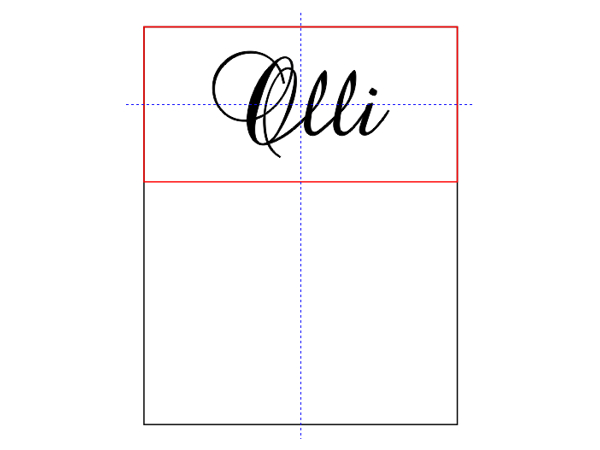
Nun soll der Schreiber noch eine Lasergravur erhalten. Dafür wird zunächst eine Laser-Datei erstellt, die die Schrift über den Umfang des Schreibers abrollt.
Fertigung eines Kugelschreibers (24/27)
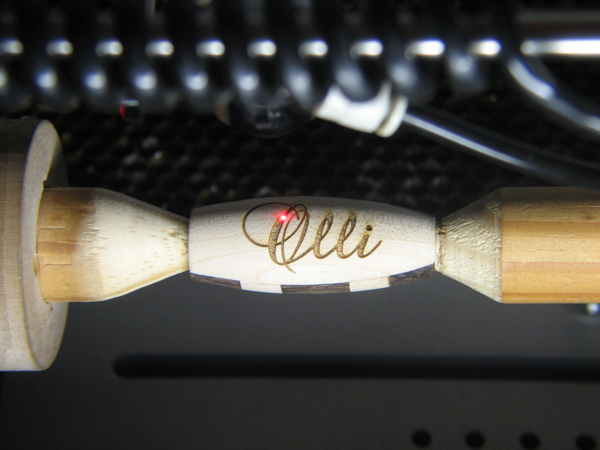
Dieser Entwurf wird dann im Laser mit einer Abrollvorrichtung ausgeführt. Die Schmauchspuren des Laserns um die Buchstaben werden wieder von Hand weggeschmirgelt.
Fertigung eines Kugelschreibers (25/27)
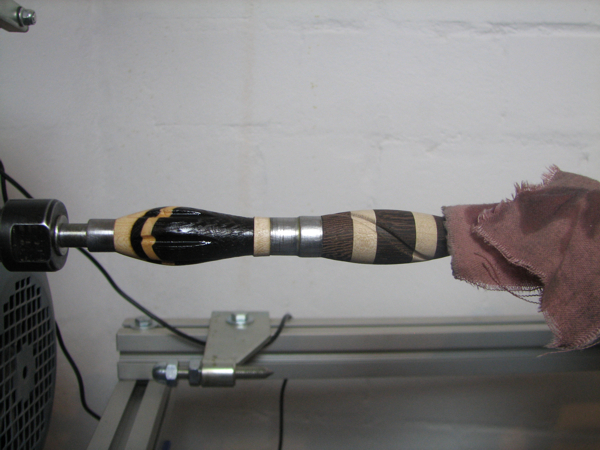
Jetzt wird eine Oberflächenversiegelung in mehreren Schichten aufgebracht. Der Unterschied zum rohen Holz ist bereits nach der ersten Schicht nicht zu übersehen. Damit ist der Schreiber später gegen Schmutz und Handschweiß beim Schreiben gut geschützt.
Fertigung eines Kugelschreibers (26/27)
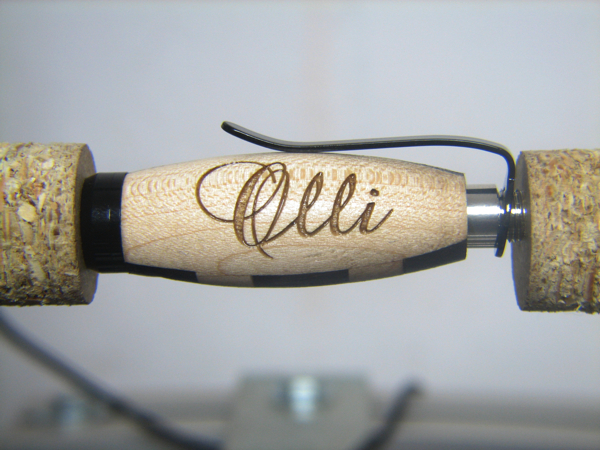
Nun kommt Olli mächtig unter Druck. Das bedeutet, dass die Kugelschreiber-Mechanik jetzt auf bzw. in die Holzteile gepresst wird. Diese Verbindung ist so stark, dass nicht geklebt werden muss.
Fertigung eines Kugelschreibers (27/27)
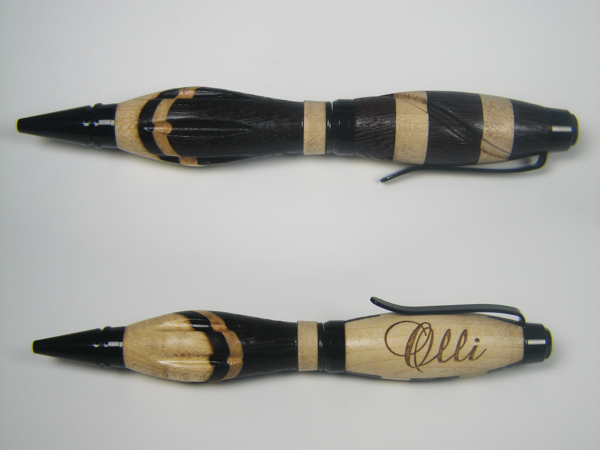
Nach diesen letzten Arbeitsschritten ist der Kuli nun zusammengebaut, damit fertig und bietet als Unikat eine buchstäblich "einmalige" Vorder- und Rückseite.
Fertigung eines Schlagbleches für eine Gitarre mit persönlicher Unterschrift
Fräsen einer Ehrenmedaille mit Bild aus eloxiertem Aluminium